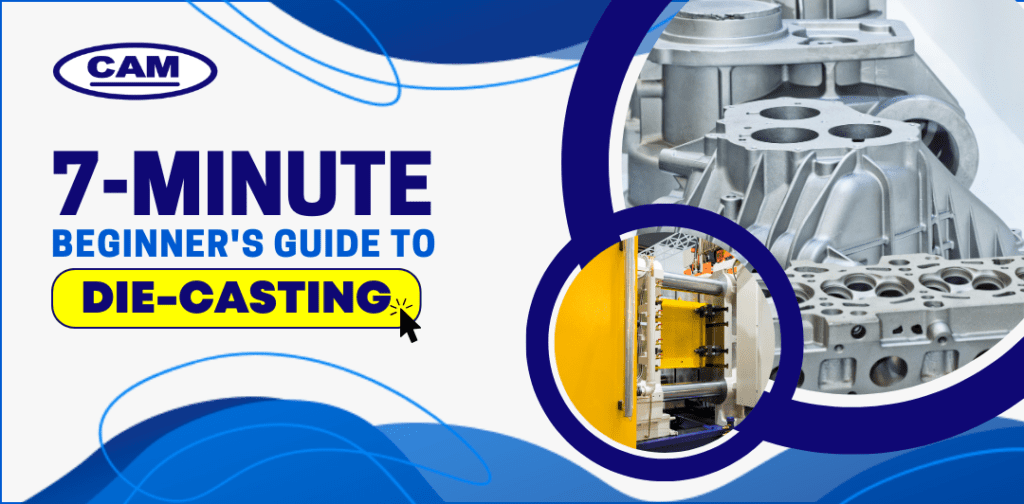
Ever wonder how that zipper on your jacket or the gears in your bike got there? Well, let’s turn to the magic technique that shapes everyday life – die-casting. Hot stuff goes in, cool stuff comes out – it’s as simple as that!
Die-casting is a manufacturing process where liquid metal meets high pressure, transforming into components that drive innovation across countless industries. The molten metal dances to the tune of precision, solidifying into intricate shapes with breathtaking accuracy.
Intrigued? But how does die-casting work? What are the secrets behind its precision and efficiency? And what breathtaking creations can be born from this fiery dance? Well, there are answers!
In this blog, we’ll delve deep into its core principles, explore its diverse applications, and unveil the application of its remarkable accuracy.
What is Die-Casting and How Does it Work?
Die-casting is a prominent machining process that stands out among various manufacturing techniques. It involves injecting molten metal into a custom-designed mold, known as a die, to create highly detailed and precise components.
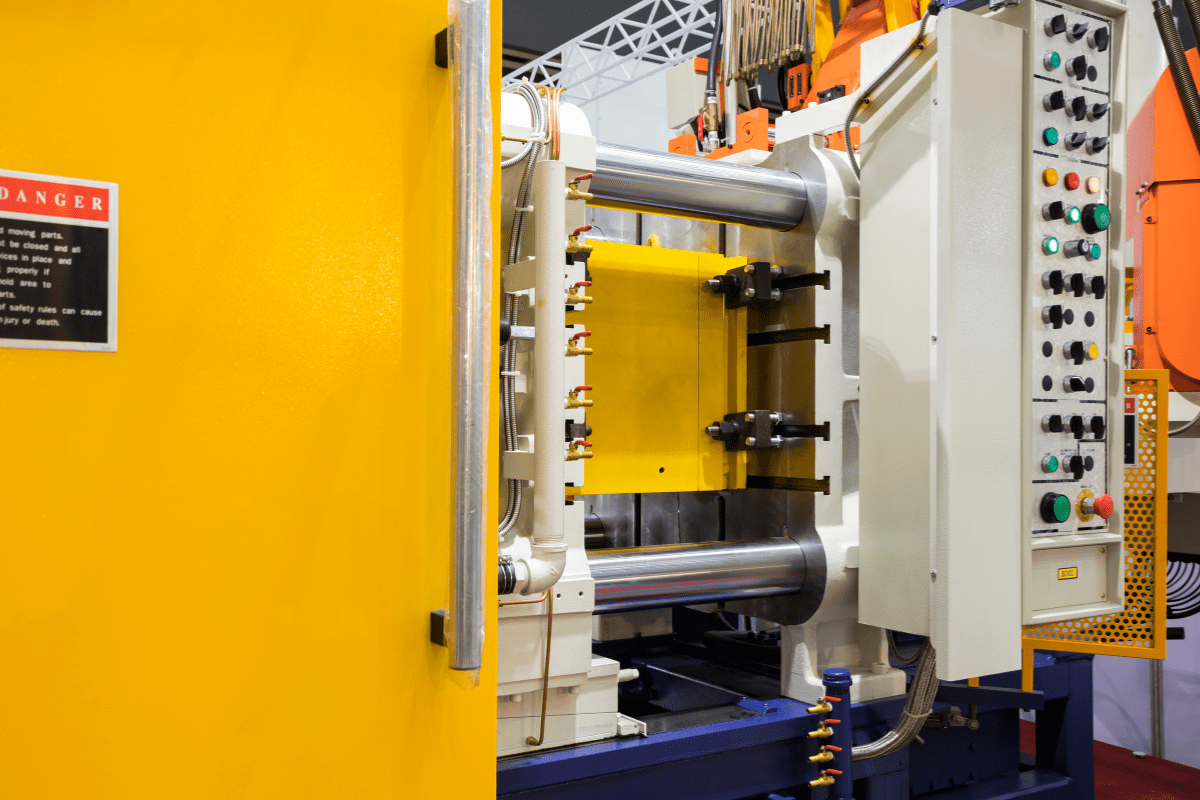
The die is made in two halves and creates a precise, reusable mold for the desired part. The process begins with the preparation of the die halves, which are then clamped together. Due to their low melting points, molten metal, usually aluminum, zinc, or magnesium, is injected into the die cavity under immense pressure, ranging from hundreds to thousands of pounds per square inch.
The high pressure ensures that the molten metal fills the entire mold quickly and accurately, creating detailed parts with tight tolerances. Once the metal solidifies within the die, the mold opens, allowing the finished part to be ejected.
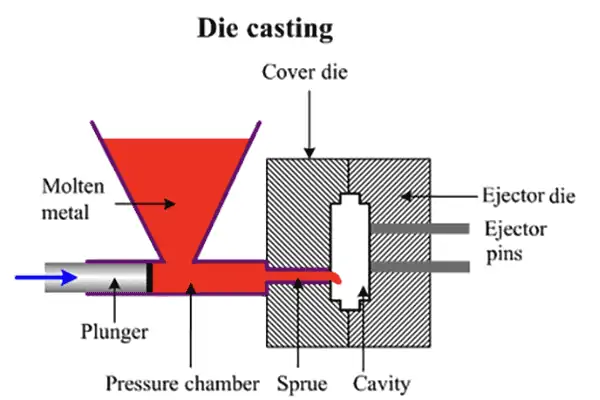
Die-casting offers unique advantages compared to other machining processes such as milling or turning. It allows for producing complex shapes with intricate details that would be challenging to achieve through traditional methods. The high-pressure injection of molten metal into the die ensures excellent dimensional accuracy and repeatability, resulting in consistent quality parts.
Let’s discover how this technique has revolutionized manufacturing by delivering intricate, high-quality components with precision and efficiency.
The Evolution of Die-casting
The history of die-casting can be traced back to ancient times when copper and bronze were used to create intricate objects and decorative items. However, it wasn’t until the 19th century that the modern die-casting process was developed.
In 1838, the first die-casting machine was patented by Sturges in the United States, which used a hand-operated plunger to inject molten lead into a die.
The first commercial application of die-casting was for the production of printing type in the early 20th century. This process revolutionized the printing industry, enabling the mass production of types with consistent quality and precision.
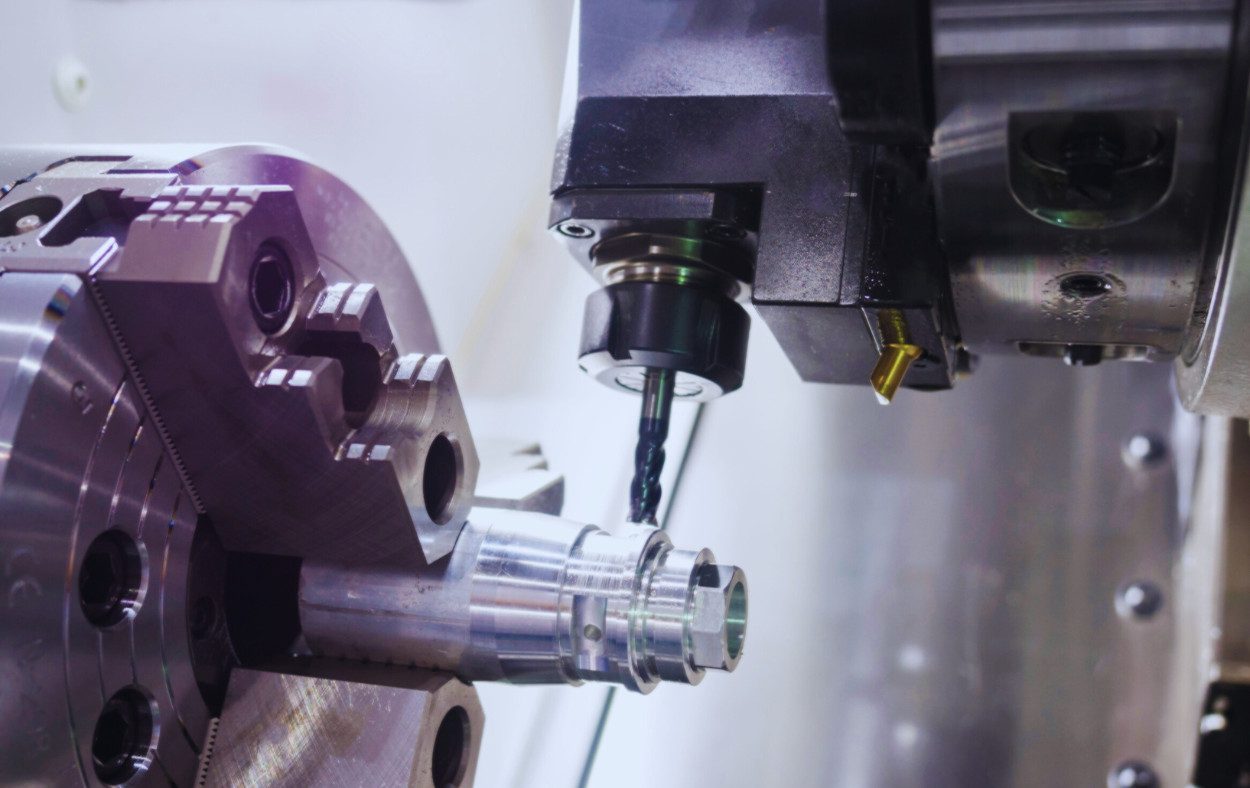
During World War I, die-casting became a method for producing military equipment and weapons, used to create intricate parts for aircraft engines, machine guns, and other military hardware.
Die-casting is a critical manufacturing process used in automotive, aerospace, electronics, and other industries. With advancements in technology and materials, die-casting continues to evolve, unlocking new possibilities for creating complex components with unmatched quality and efficiency.
Types of Die-casting
Die-casting encompasses two main types of processes, each tailored for different metal characteristics and requirements:
1. Hot Chamber Die-Casting:
In this method, the die is immersed in a bath of liquid metal, ready to be transformed into the desired shape. With the aid of a hydraulic piston, the molten metal is injected into the die cavity, filling it meticulously. This process is particularly suited for metals with lower melting points, such as zinc, tin, and lead.
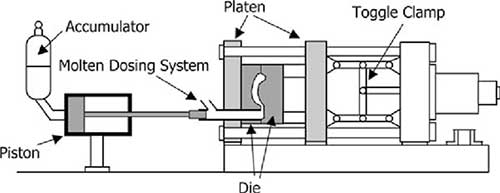
The advantage of hot chamber die-casting lies in its efficiency and rapid production speed. Keeping the metal in a molten state within the machine eliminates the need for external melting furnaces, streamlining the manufacturing process.
2. Cold Chamber Die-Casting:
In cold chamber die-casting, the molten metal is not directly in contact with the die. Instead, it is melted in a separate furnace and then ladled into a cold chamber.
From there, a hydraulic piston injects the molten metal into the die cavity under high pressure. This process is commonly used for metals with higher melting points, such as aluminum, copper, and magnesium.
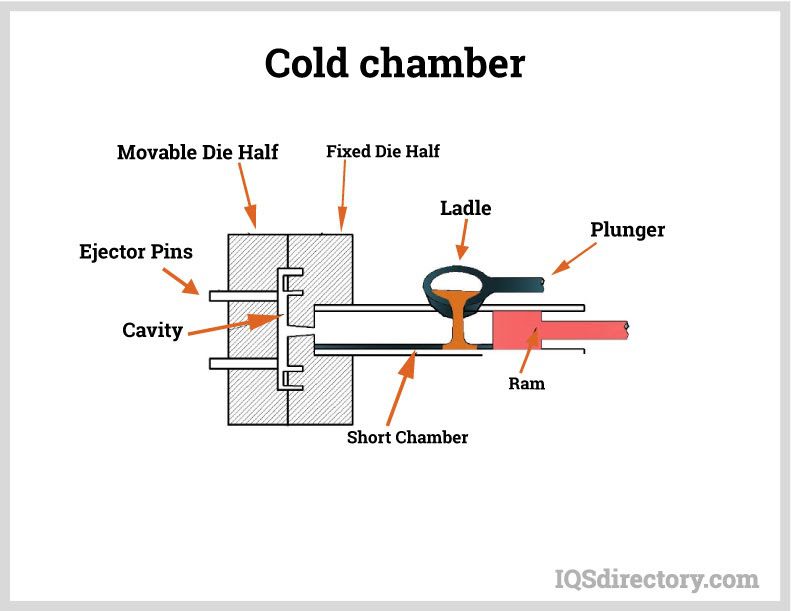
The advantage of cold chamber die-casting is its ability to handle metals that would erode or react with the hot chamber’s materials.
By understanding the distinctions between hot chamber and cold chamber die-casting, manufacturers can select the appropriate method based on the specific metal properties and desired end product. These techniques enable the precise and efficient production of intricate metal components that meet the demands of various industries.
Why Die-casting?
Die-casting stands out as a manufacturing process, offering a multitude of advantages that make it a preferred choice across industries:
High Precision:
One of the primary advantages of die-casting lies in its ability to fabricate parts with complex geometries and thin walls, making it an ideal choice for various applications across industries.
Moreover, the high degree of dimensional accuracy achieved through die-casting significantly reduces the need for additional machining processes, streamlining production timelines and minimizing associated costs. Additionally, die-cast components are renowned for exhibiting superior mechanical properties and exceptional surface finishes, often obviating the necessity for secondary finishing operations.
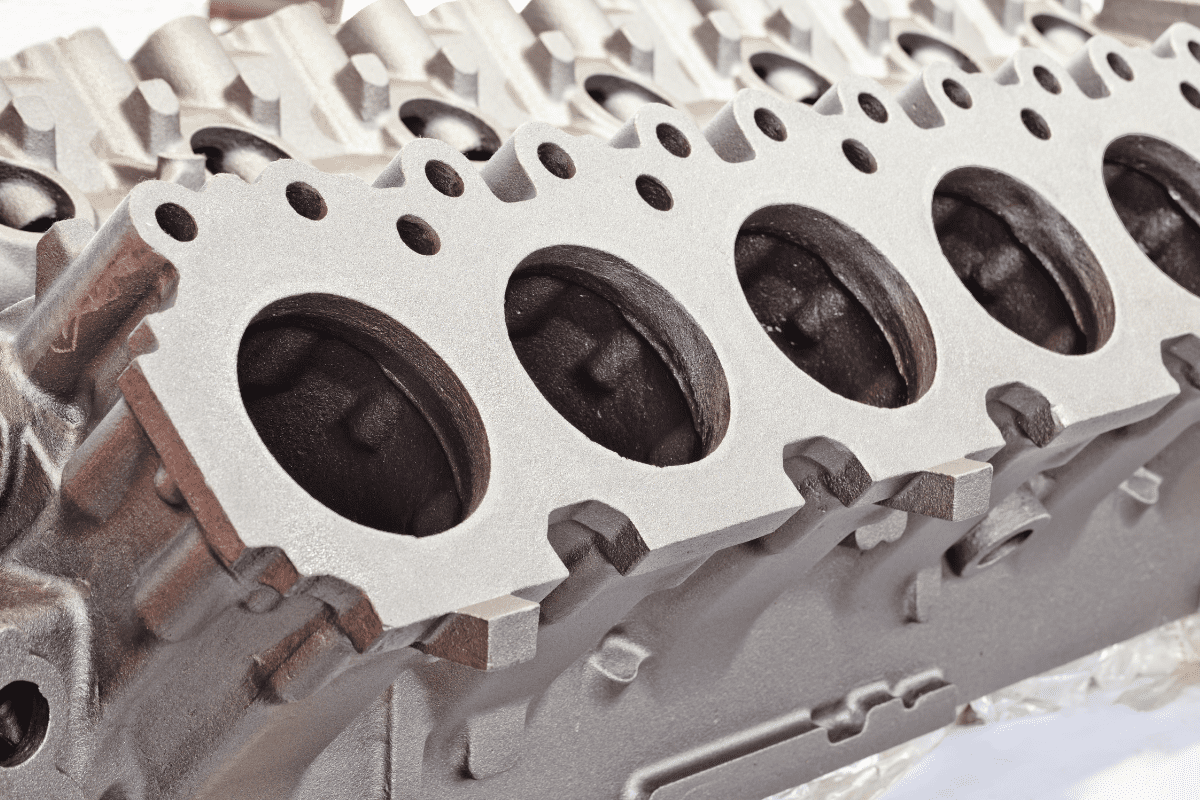
This unparalleled level of precision and consistency renders die-casting the preferred method for producing high-quality components utilized in demanding industries such as automotive, aerospace, and electronics.
Cost-Efficiency:
By enabling the creation of intricate shapes with tight tolerances at high speeds, die-casting facilitates the rapid production of a large number of parts, meeting the demands of mass production while maintaining efficiency. The reduced material waste not only aligns with sustainable manufacturing practices but also translates into tangible cost savings for businesses, besides assuring high-quality components.
Strength and Durability:
Die-cast parts are also renowned for their exceptional strength-to-weight ratios, which enable them to be lightweight while maintaining robustness. These components are highly capable of enduring challenging operating conditions, such as high temperatures and mechanical stress, without sacrificing their integrity.
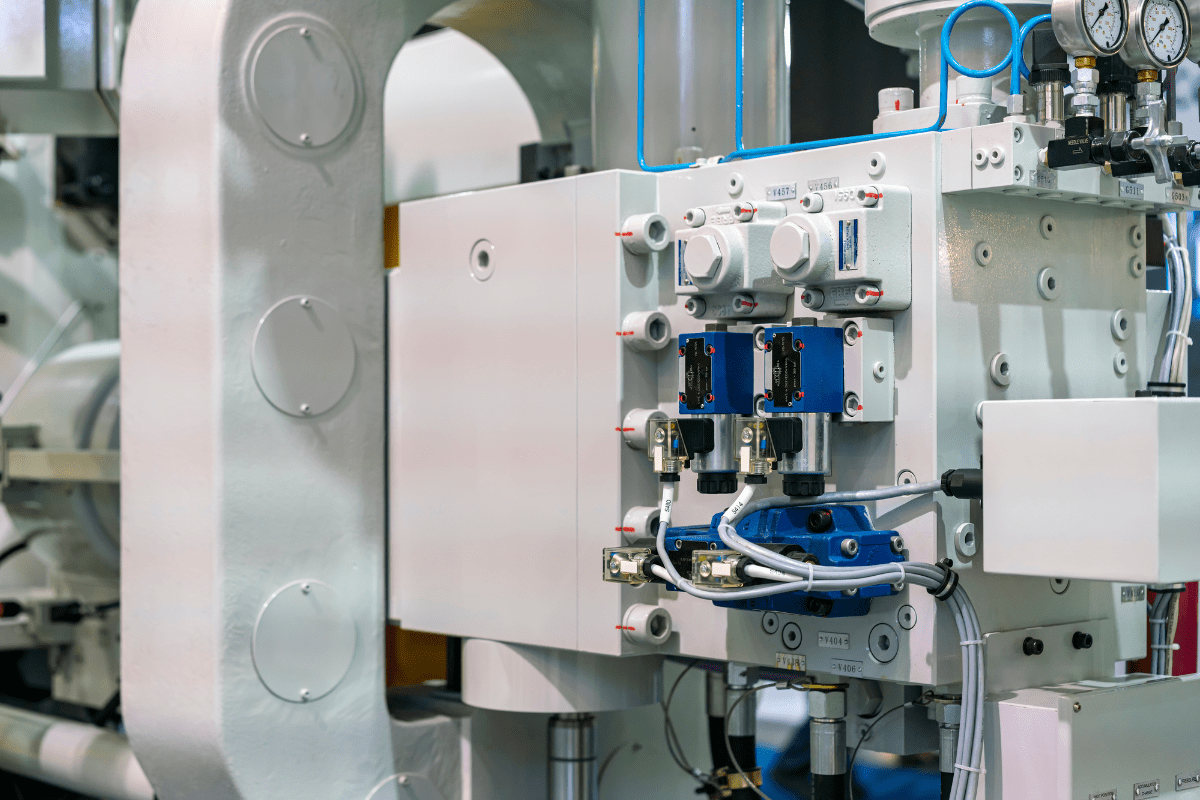
This unique combination of strength and lightness makes die-cast parts a preferred choice for various industrial applications, where durability and performance are critical.
Versatility:
Die-casting is a versatile manufacturing process that can accommodate a wide range of metals and alloys, including aluminum, zinc, magnesium, and copper.
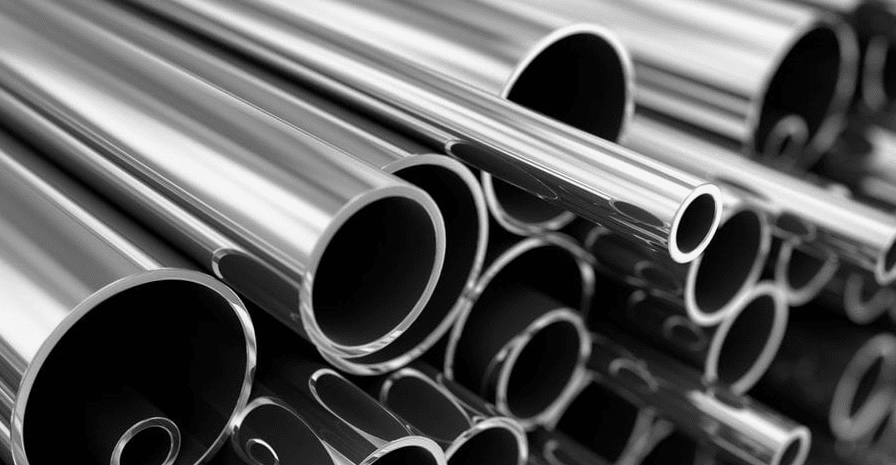
This allows manufacturers to select the most suitable material for their specific application, considering various factors such as strength, weight, corrosion resistance, and thermal conductivity. For example, aluminum is often chosen for its lightweight properties and corrosion resistance, making it suitable for applications where weight reduction and durability are important.
Die Casting’s Application Across Industries
Die-casting proves its worth across a wide range of industries, showcasing its adaptability and reliability:
Electronics:
The electronics industry leverages die-casting for its capability to create parts with outstanding heat dissipation properties. Devices such as smartphones, laptops, and gaming consoles integrate die-cast components for their durability and effective thermal management, contributing to enhanced performance and reliability.
Automotive:
Die-cast parts are integral to the automotive sector, serving in vital roles within engine components, transmission housings, and structural parts. The exceptional strength and precision of die-cast components significantly enhance the performance and durability of vehicles, underscoring their critical importance in ensuring the reliability and functionality of automotive systems.
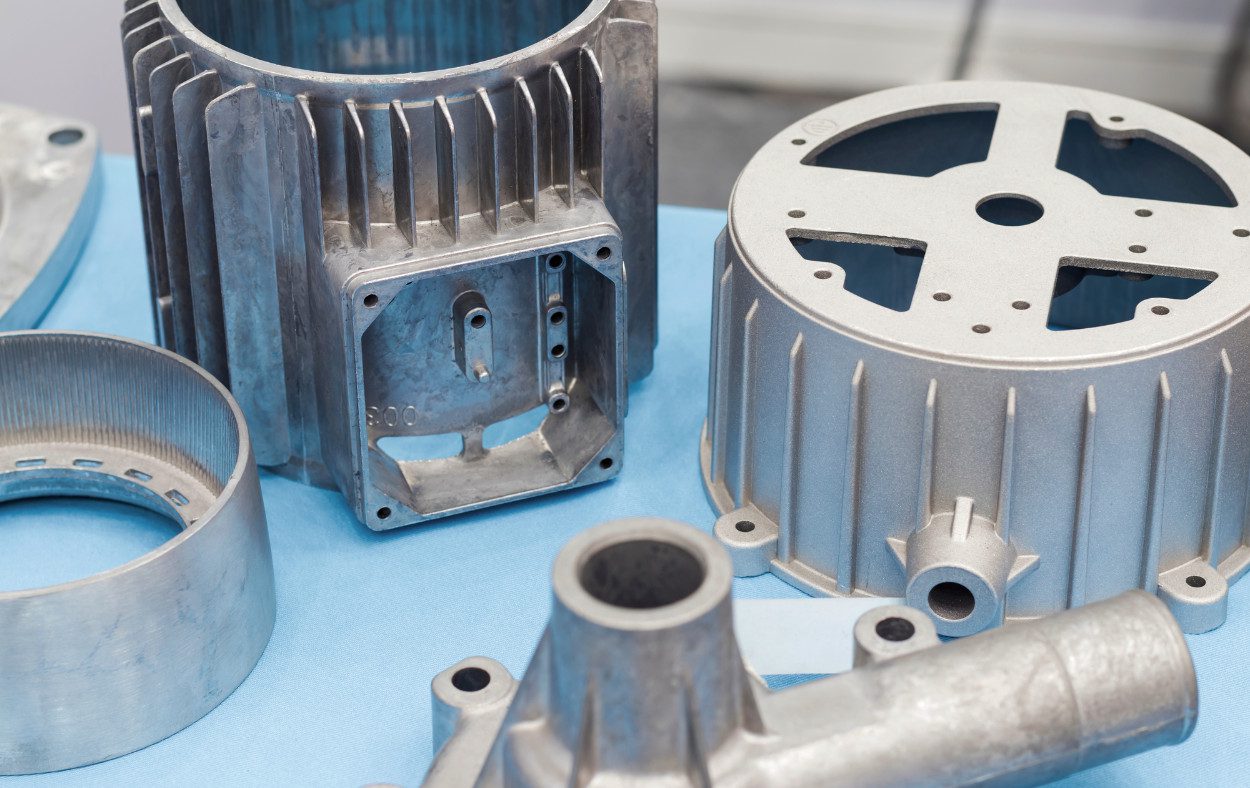
Aerospace:
In the aerospace industry, die-cast components are utilized in critical areas such as aircraft engine parts, landing gear components, and structural elements. The high strength-to-weight ratio of die-cast parts makes them ideal for ensuring performance and safety in aircraft applications.
Home Appliances:
Household appliances rely on die-cast parts for their strength, durability, and aesthetic appeal. From refrigerators and washing machines to air conditioners, die-cast components enhance the functionality and visual appeal of these everyday appliances.
Embracing die-casting technology empowers industries to create robust, precise, and visually pleasing components that meet the demands of diverse applications. With its versatility and proven track record, die-casting continues to be an indispensable manufacturing method across multiple sectors.
Discover the World of Precision Manufacturing!
Beyond the realm of die-casting, precision tooling manufacturing boasts a vast array of sophisticated machining techniques and processes meticulously designed to achieve the pinnacle of precision. This intricate world offers a multifaceted approach to crafting molds, ensuring unwavering adherence to the tightest tolerances and delivering unmatched levels of accuracy.
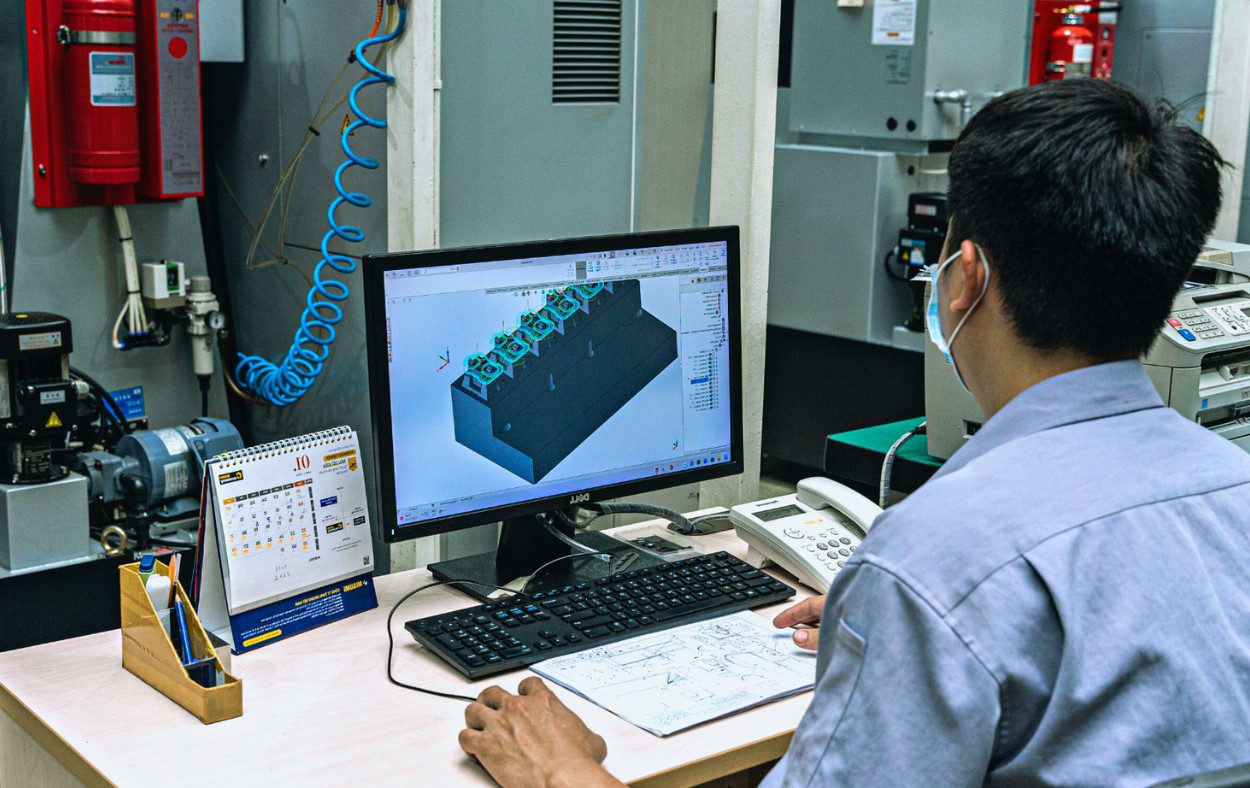
With years of proven expertise in precision tooling, CAM Resources is home to comprehensive precision mold and die solutions for manufacturers. CAM Resources ensures top-tier precision and unparalleled accuracy and always delivers timely delivery. You can check out our exclusive products page for die components by clicking here.
If you enjoyed reading this blog, enter our illuminating blogosphere, where we dissect fascinating topics ranging from the intricate workings of EDM (Electrical Discharge Machining) to the artistry of precision machining.
Check out our blog page now, a treasure trove of knowledge, unlocking new insights and perspectives.
Minh Ngoc Truong
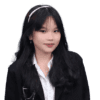
Hi, I'm Minh Ngoc, a dedicated blog writer and social media manager at CAM Resources.