Read our blog on CNC milling to learn how this versatile technique can produce precise and complex geometries with ease, delivering consistent and high-quality results that meet your exact requirements.
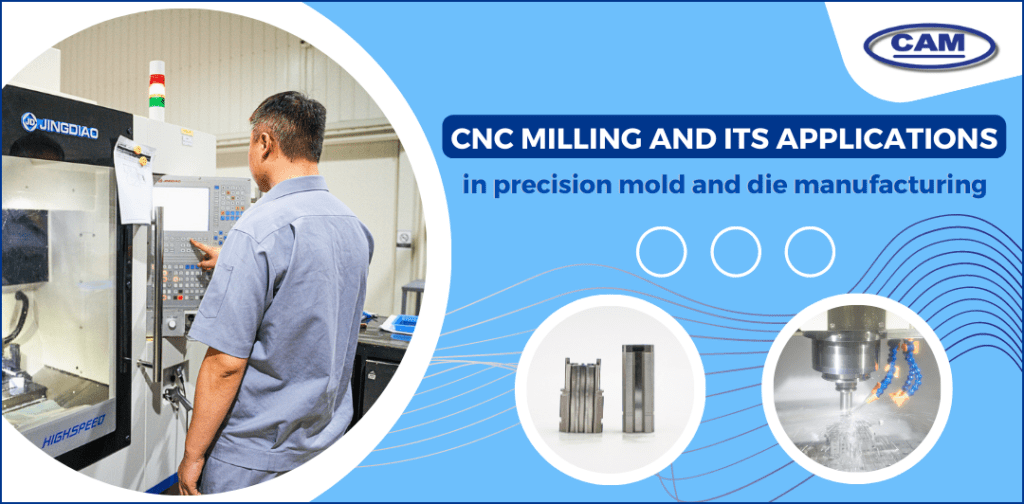
We are in an era where, regardless of the sector, businesses must be constantly on the lookout for ways to increase productivity and efficiency, especially when it comes to day-to-day operations, supply chains, and manufacturing processes. We’ve seen workplaces transformed by AI-powered technology, and in this evolution, time-consuming processes are being automated.
Let’s take one step back to the factories, where the shop floors have enhanced productivity, employing cutting-edge machining capabilities. And if we talk about precision engineering, with the appearance of CNC milling machines, high-precision tooling, mold making, and die making have never been easier. Being the industry under the layer, the impact can be felt across various industries, ranging from aerospace to electronics to automotive to medical devices.
CNC machines offer a range of benefits that traditional machining techniques simply cannot match. From producing complex shapes and patterns to improving accuracy and repeatability, CNC milling machines have truly revolutionized manufacturing.
In this blog post, we’ll take a closer look at how CNC milling machines are being used in precision mold and die making. Starting off with the basics, we’ll explore the various types of these machines and their applications in detail.
What is a CNC Milling Machine?
A CNC milling machine is nothing less than an engineering wonder, capable of creating precise and complex shapes from raw materials like metal and plastic. Many components make up a CNC milling machine, including the spindle, which holds the cutting tool, and the worktable, which holds the cut material.
The machine also has a control panel, which is used to program the toolpath and adjust the machine’s settings. Other main components include the coolant system, which keeps the cutting tool from overheating, and the chip conveyor, for waste material removal. These parts work together as a powerful and versatile machine that can carve everything from simple parts to complex prototypes.
CNC refers to computer numerical control, and these machines work by using a combination of computer programming and mechanical processes. Technicians start by inputting a digital file containing instructions to the control panel of the machine on how to shape the workpiece.
These instructions are then converted into a series of coded signals that the machine’s motors and actuators utilize to move and rotate the cutting tool accurately. Then, the cutting tool of the CNC milling machine will remove excess material from the workpiece until it is precisely shaped into the desired form.
CNC vs. Manual Milling
The primary difference between manual milling machines and CNC milling machines is the level of automation involved in the process. For manual milling, a technician physically adjusts the machine’s movements and cutting tools. It requires an operator to physically turn handles and levers to position the workpiece and move the cutting tool through the material. Manual milling is a cost-effective option for manufacturing small batches of components and is easier to use.
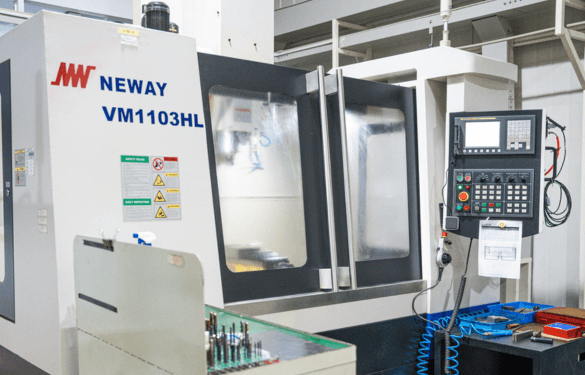
On the other hand, a CNC milling machine is entirely computer-controlled, and it uses precision software, codes, and automated movements to shape and cut materials. It requires little to no manual intervention. CNC milling machines are highly accurate and can produce complex shapes and intricate parts to tight tolerances. It provides improved efficiency and consistency in the manufacturing process, reduces errors and waste, and allows the production of customized products at a faster rate.
CNC Milling for Precision Molds & Dies
In the field of precision mold and die manufacturing, the CNC milling process plays a crucial role in bringing out the best quality in every single mold and die workpiece. The milling process begins with Computer-Aided Design (CAD) software, where designers create precise 3D models of the mold or die. The engineer then moves on to the Computer-Aided Manufacturing (CAM) programming stage, where they can refine the design through digital simulation and refine the parameters to make it efficiently machineable.
Once the design is optimized, the tools are selected, the materials are carefully chosen, and the machining process begins. The CNC milling machine will use the CAD file to achieve consistently accurate cuts into the selected material. The high precision of the cutting process ensures that the exact specifications required by the design are achieved, in the form of a high-quality mold or die.
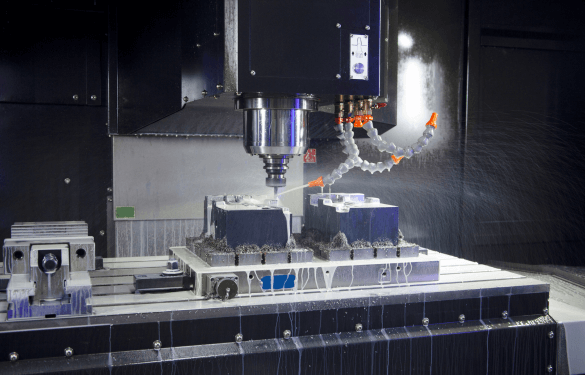
Throughout the machining process, the operator monitors the machining and makes adjustments as necessary. The result is a highly precise and accurate machined part with tight tolerances and superior surface finishes that meets or exceeds design specifications.
3 Most Common Types of CNC Milling Machines
Several different types of CNC milling machines are used in many industries, such as automotive, medical, precision mold, and die making. These include vertical milling machines, horizontal milling machines, and 5-axis milling machines. Each of these machines has its own unique advantages and disadvantages, and the choice of machine will depend on the specific needs of the manufacturer.
CNC Vertical Milling
A CNC vertical milling machine is a powerhouse tool in the machining industry. Its main function is to shape various materials through the use of a rotating cutter, which moves up and down along the vertical axis. This machine is incredibly versatile and can create complex shapes and designs with ease. It’s perfect for drilling, cutting, and shaping materials such as metal, wood, and plastic.
1. CNCTech
2. CAM Resources
CAM Resources has the right precision EDM, wire-cutting, grinding machines that can meet customer’s exact engineering specifications. As proof of the company’s excellent work in the industry, CAM Resources is the first foreign company to be awarded the Certificate of Science & Technology Enterprise by the People’s Committee of Long An Province.
CAM Resources also offers worldwide shipping of finished products in a timely and hassle-free fashion. It is one of the best choices for clients who are looking for surface grinding service that inherits foreign technology for a competitive pricing plan.
CNC Horizontal Milling
On the other hand, a horizontal milling machine features a cutting tool mounted horizontally on the spindle, and the workpiece is positioned horizontally on the table. Horizontal milling machines are commonly utilized for more substantial machining tasks such as shaping and slotting. Moreover, they are well-suited for cutting grooves or slots in a workpiece too wide for a vertical milling machine to manage.
CNC 5-Axis Milling
A 5-axis CNC milling machine is a type of milling machine that is capable of moving the cutting tool and the workpiece on five different axes (X, Y, Z, A, and B). The A and B axes refer to two rotational axes simultaneously. With this additional flexibility, the cutting tool can approach the workpiece from any direction or angle, which enables complex geometries to be machined with high precision.
General Applications of CNC Milling Machines
Given their precision and accuracy in producing intricate parts and shapes, CNC milling machines are often used in a variety of manufacturing industries, from aerospace, shipping, automobiles, oil drilling, pumping, and refining to medical, FMCG manufacturing, and precision engineering sectors.
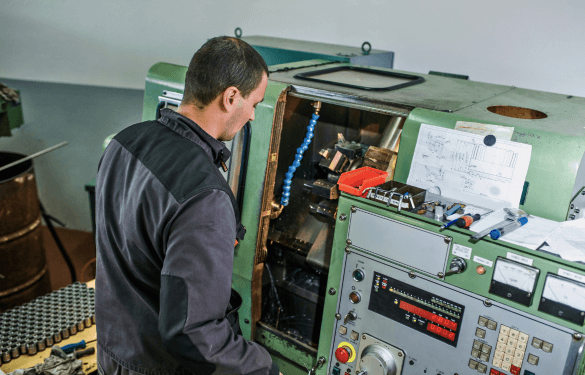
Different parts that a CNC milling machine can work on include aerospace components such as landing gear components and fuselage structures. Also control panels, axles, car molds for automotive, enclosures for consumer electronics, surgical instruments and orthotics for medical, woodworking, and even machine parts for the oil and gas industry.
Why Use CNC Milling for Precision Tooling, Molds and Dies?
This process requires a high degree of accuracy, which can be difficult to achieve using manual machines. However, thanks to computer numerical control (CNC) milling machines, manufacturers can now produce parts with the precision and accuracy required with less effort. Additionally, CNC milling machines offer a considerable edge over traditional machines regarding precision mold making, including increased precision, efficiency, productivity, repeatability, and consistency.
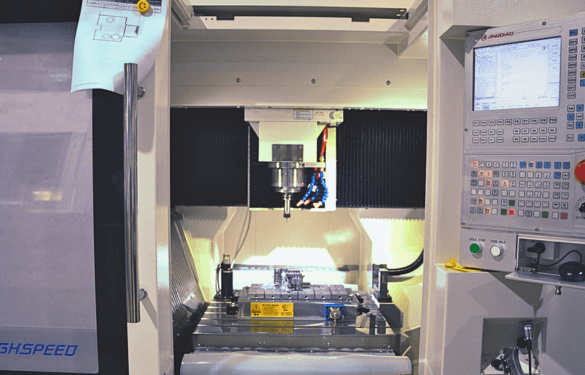
1. Precision first
CNC milling machines use computer-aided design (CAD) and computer-aided manufacturing (CAM) software to create 3D renderings of the molds and dies and then use this data to make precise cuts to the workpiece. Therefore, the results come with extremely high levels of accuracy, ensuring that each cut is made to precise specifications.
2. Increased efficiency and productivity
Also, CNC milling machines can create complex shapes and geometries easily, increasing efficiency and productivity. This way, by running CNC milling machines for extended periods with less human intervention, manufacturers can maximize productivity while minimizing downtime due to human error or fatigue.
3. Consistency and repeatability
Ultimately, the consistency of CNC milling machines makes them indispensable tools for manufacturers in the precision mold and die industry. Using CNC milling machines eliminates the scope for human errors, resulting in consistent outcomes.
The machines’ software maintains the accuracy and repeatability of the operation, ensuring that the process and the product delivered are consistent every time, which is critical in the mold and die industry.
Maintenance and Safety of CNC Milling Machines
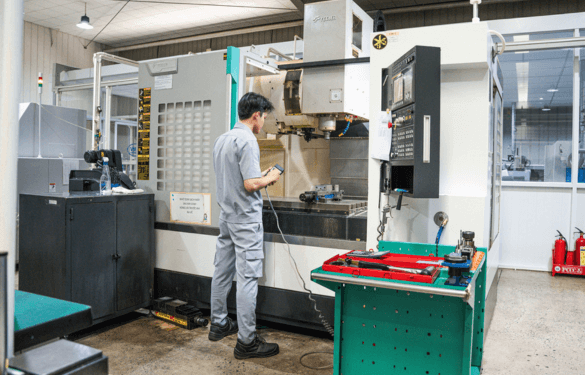
When it comes to CNC milling machines, safety should always be top of mind. When operating a CNC milling machine. Always use proper protective gear, such as safety glasses and gloves, and follow all safety guidelines and procedures to avoid injury. By taking care of your CNC milling machine and practicing good safety habits, you can ensure that it continues to operate smoothly and efficiently for years to come.
These machines are powerful tools that can create precise and complex parts, but just like many other machines, the more we take care of them, the more they return the favor. Maintenance tasks like cleaning, lubricating, and replacing worn parts can help prevent breakdowns and extend the lifespan of your CNC milling machine, benefiting your business in the long term.
Choosing CAM Resources for Your Precision Needs
In conclusion, CNC milling machines have revolutionized the precision mold and die-making industry. With their unparalleled accuracy, speed, and efficiency, they have made it possible to produce complex and intricate parts with ease. Whether you’re a well-established business or a new entrant in the manufacturing field, investing in a quality CNC milling machine is a smart decision that will pay off in the long run.
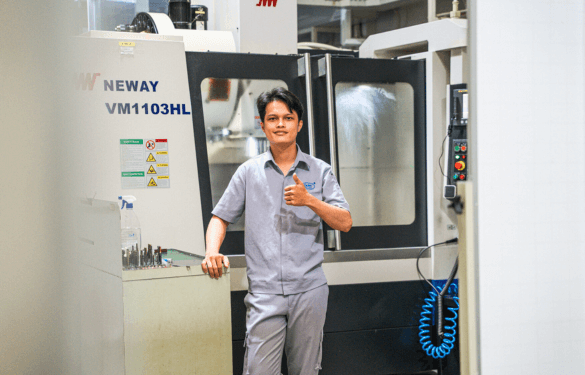
If you’re looking for high-quality precision tooling, molds, and dies processed with the latest machining technologies, look no further than CAM Resources! Our CNC milling machines are precision-engineered to deliver superior results for your tooling, mold, and die requirements.
At CAM Resources, we are equipped with cutting-edge technologies. Yet, it’s a mix of man and machine! Our skilled technicians and exceptional customer service team are always by your side, exacting your engineering specifications right on time. For more information on our machining expertise, check out our technology web page to see how we can help you achieve precision! Also, we employ the latest EDM technologies alongside milling and you may review our last blog demonstrating our expertise in EDM machining, both electrode and wire cut.