Injection molding is a manufacturing process that enables the production of intricate and high-quality plastic parts. But many will start to question once they know the price tag on a singular injection mold. Reading this blog will let you understand the real reasons behind expensive injection molds, and a few alternative options to decide what fits better for your manufacturing needs.
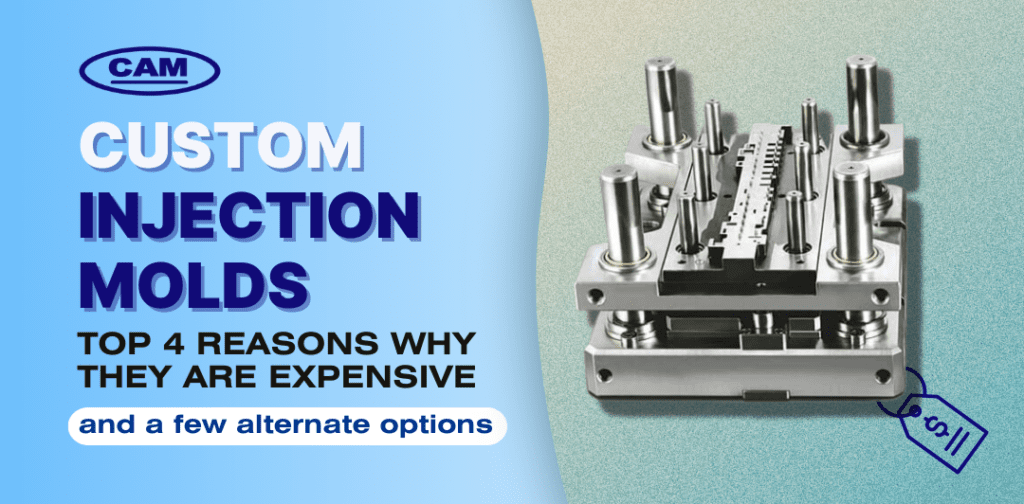
Have you ever wondered how your earpod cases are made? It’s not one, it’s not two, but they are to be produced in hundreds of thousands to meet the market demands. Thanks to machine tools, essentially the precision molds of the injection molding machines, enable manufacturers to mass produce these consumer products.
The same applies when it comes to producing complex car parts. However, getting your hands on one of these custom-made machine tools can be quite costly. We will soon discover what injection molds are, and why they are so high-priced.
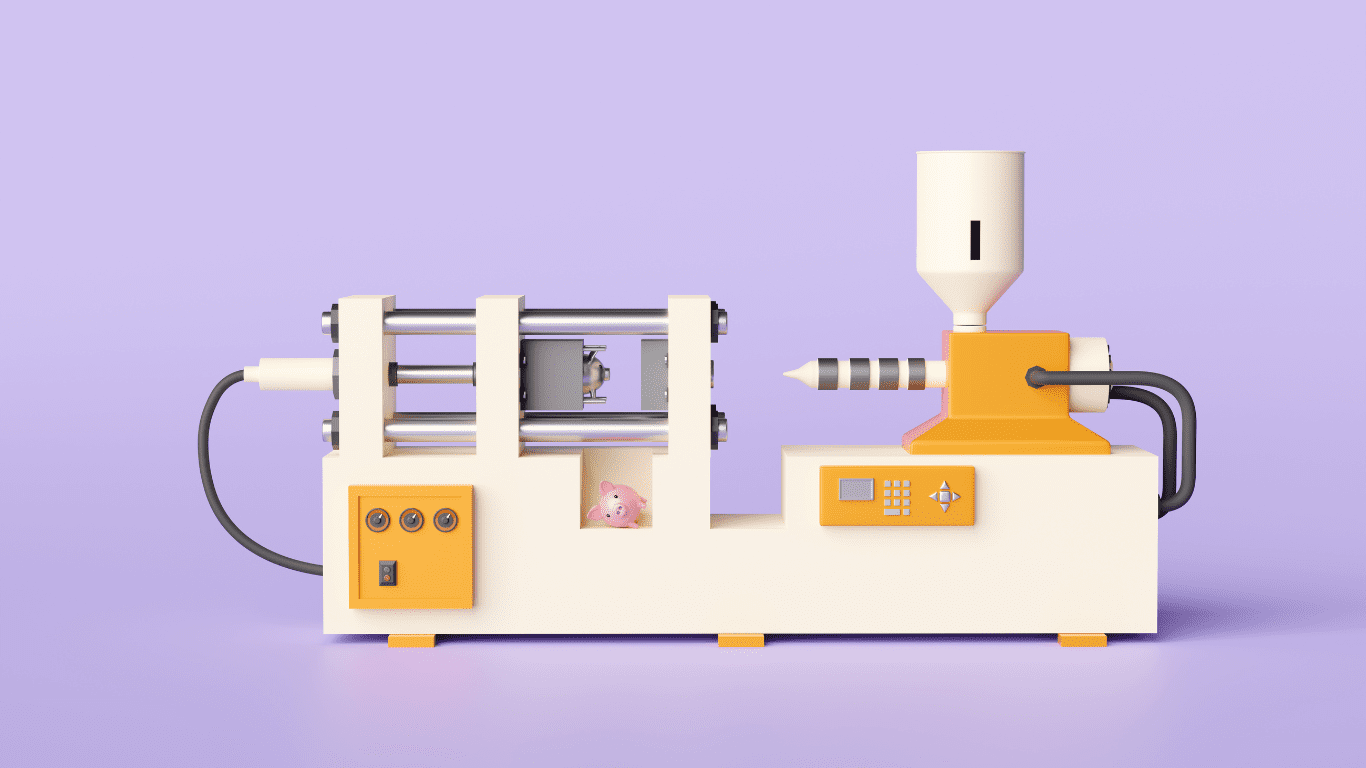
Injection molds play an indispensable role in the plastic manufacturing industry, enabling the mass production of high-quality plastic products with speed and precision. These molds are custom-made according to the specific design requirements of a product and will be later used for the mass production of identical parts. Usually made from high-quality steel or aluminum, these injection molds are able to withstand the high pressures and temperatures involved in the injection molding process.
In this quick reading, we will explore the concept of injection molds, their wide-ranging applications across industries, and the advanced technologies used in their manufacturing process.
Applications of Injection Molding
Injection molds are essential tools with applications spanning across various industries, making them an essential component of modern manufacturing. Below are some references:
Automotive
Injection molds play a vital role in producing automotive components, including interior and exterior trims, dashboards, door panels, and engine parts. The ability to create complex shapes and consistent parts makes injection molding indispensable in the automotive sector.
Electronics
Injection molds are widely used in the production of consumer goods, such as household appliances, packaging, toys, and electronic devices. The versatility of injection molding allows for the efficient production of intricate designs, ensuring high-quality products for consumers. One incredibly common application that most, if not all of us, know about is for making connectors.
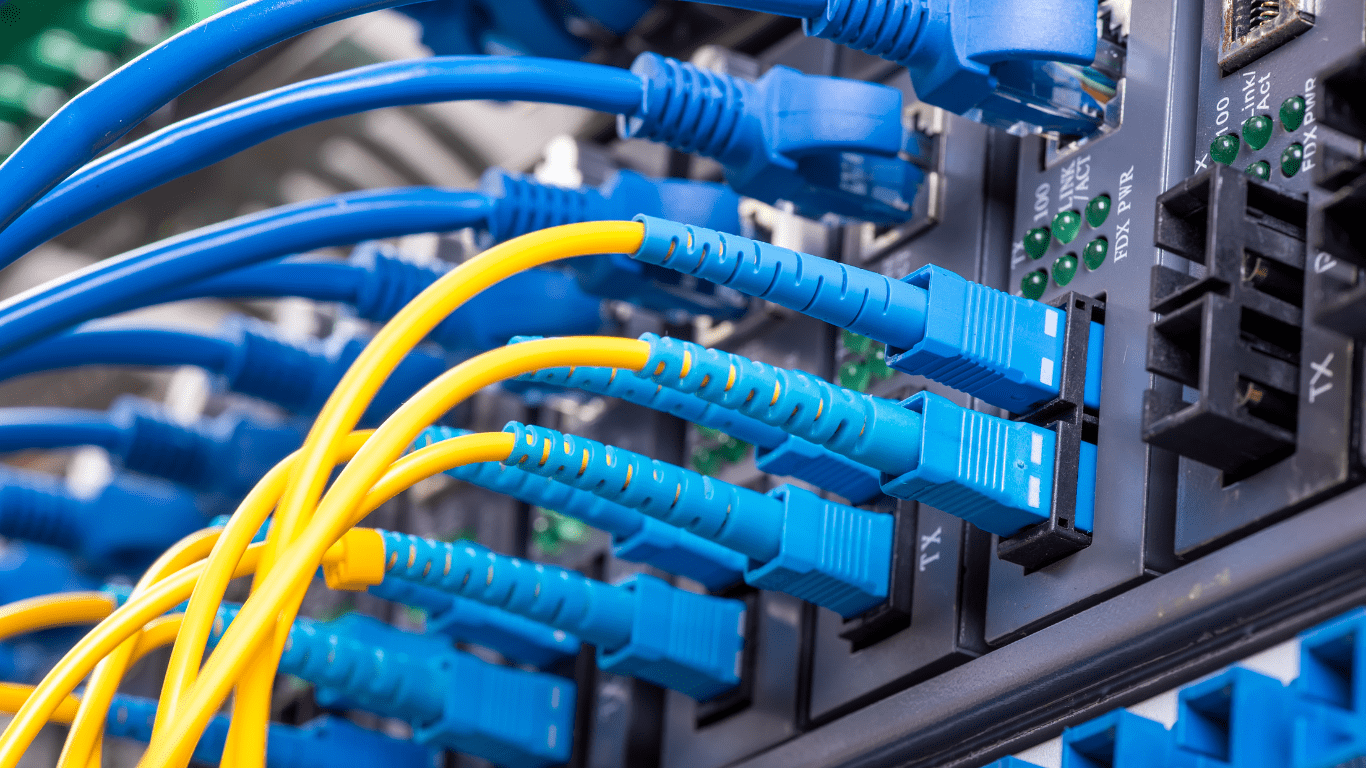
Medical and Healthcare
Precision and cleanliness are crucial in the medical and healthcare industry, and injection molds excel in meeting these requirements. They are utilized in the production of medical devices, diagnostic equipment, and surgical instruments, ensuring the highest level of precision, reliability, and safety.
So Why Are Injection Molds So Expensive?
Now, let’s hit on the core and find out why injection molds might cost you a leg despite being the mainstream option. Custom injection molds can go for anywhere for as cheap as $100, and as pricey as $100,000 for one singular mold. Several reasons are contributing to the cost behind these exceptionally complex precision tools, some of which are:
Precision Engineering Niche
Injection molds require precision engineering and design expertise to ensure that they can produce parts with intricate details and tight tolerances. Skilled engineers meticulously design the molds, running the most complex precision machining. Futhermore, the complexity of the design process adds to the cost of the molds.
Not only that, but precision tooling and injection mold manufacturing are extremely niche industries with a great demand for exceptionally skilled technicians and workers. Sourcing talent in these fields can be challenging due to the niche nature of the industries and the need for exceptional skills. Additionally, the demand for precision tooling and injection molds can be unpredictable, making it difficult to maintain stable production levels. This contributes to higher costs, as the seasonal nature of the job requires companies to manage resources efficiently.
Machining and Technologies
The manufacturing of injection molds involves advanced machining techniques and technologies both in terms of hardware and software. Computer Numerical Control (CNC) machining is commonly used to shape the molds from blocks of high-quality materials like hardened steel or aluminum alloys. CNC machining ensures precision and accuracy, but it also adds to the overall cost of the molds due to the sophisticated machinery required.
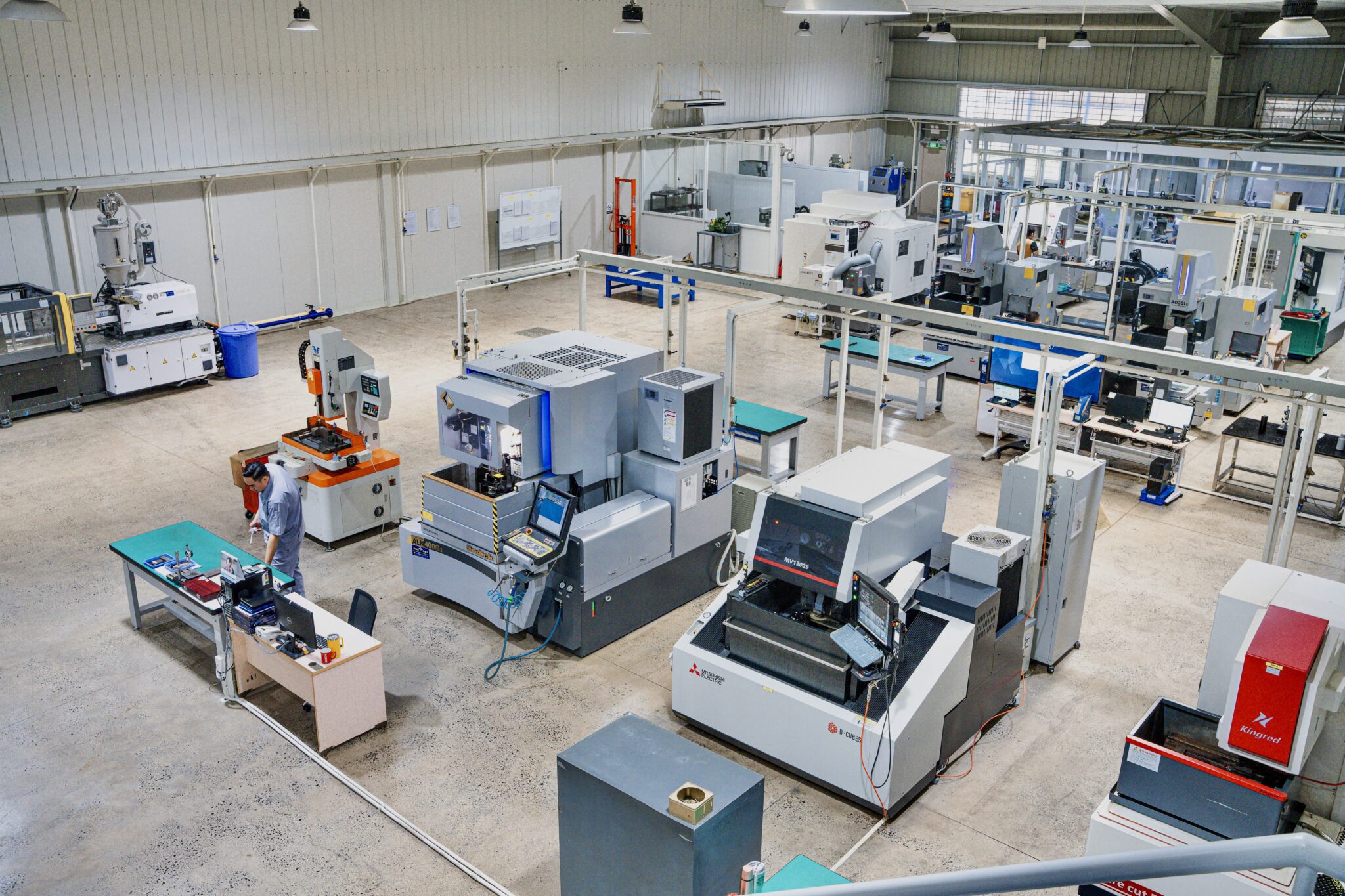
The manufacturing of injection molds involves the utilization of other advanced technologies and processes. Here are a few notable ones:
CAD/CAM Software
CAD software plays a pivotal role in designing injection molds. It allows engineers to create detailed 3D models, ensuring optimal part design, mold functionality, and manufacturability. CAD software also facilitates design modifications and iterations, reducing development time and costs.
CAD combined with CAM, the computer-aided manufacturing software, is essential for effective results in the injection molds making process. The powerful CAD/CAM software enables the operators to precisely translate 3D models into machine instructions. Running the most advanced CAD/CAM software is a matter of expertise and expense.
CNC Machining and EDM Technologies
As mentioned above, this machining is widely employed in the production of injection molds. It utilizes computer-controlled machines to precisely cut and shape the molded components from solid blocks of metal. CNC machining ensures accuracy, repeatability, and the ability to create complex features required for injection molds.
Electrical Discharge Machining (EDM) and Wire EDM are specialized processes for creating intricate shapes and fine details in injection molds. These processes involve the use of electrical sparks or a wire to erode the mold material, allowing for the creation of complex geometries and tight tolerances that may be challenging to achieve with traditional machining methods.
Material Selection and Durability
Injection molds are subjected to intense pressures and high temperatures during the injection molding process. To withstand these conditions, molds are typically made from durable materials that can endure repeated use. High-quality materials, such as hardened steel, are more expensive but offer superior durability and longevity. The choice of materials contributes significantly to the cost of the molds.
Prototyping and Rigorous Testing
Before the production phase, injection molds go through rigorous prototyping and testing to ensure optimal performance. Prototyping allows for the identification and resolution of any design flaws or issues before the mold is finalized. These crucial steps help refine the molds but also add to the overall cost of the process.
Quality control apparatus such as hardness testers, measuring microscopes, and height gauges are essential in achieving tight tolerances as precise as +/-0.001 accuracy in injection mold manufacturing. Technicians utilize these advanced tools to meticulously inspect and measure each part, going back and forth until it meets exact specifications.
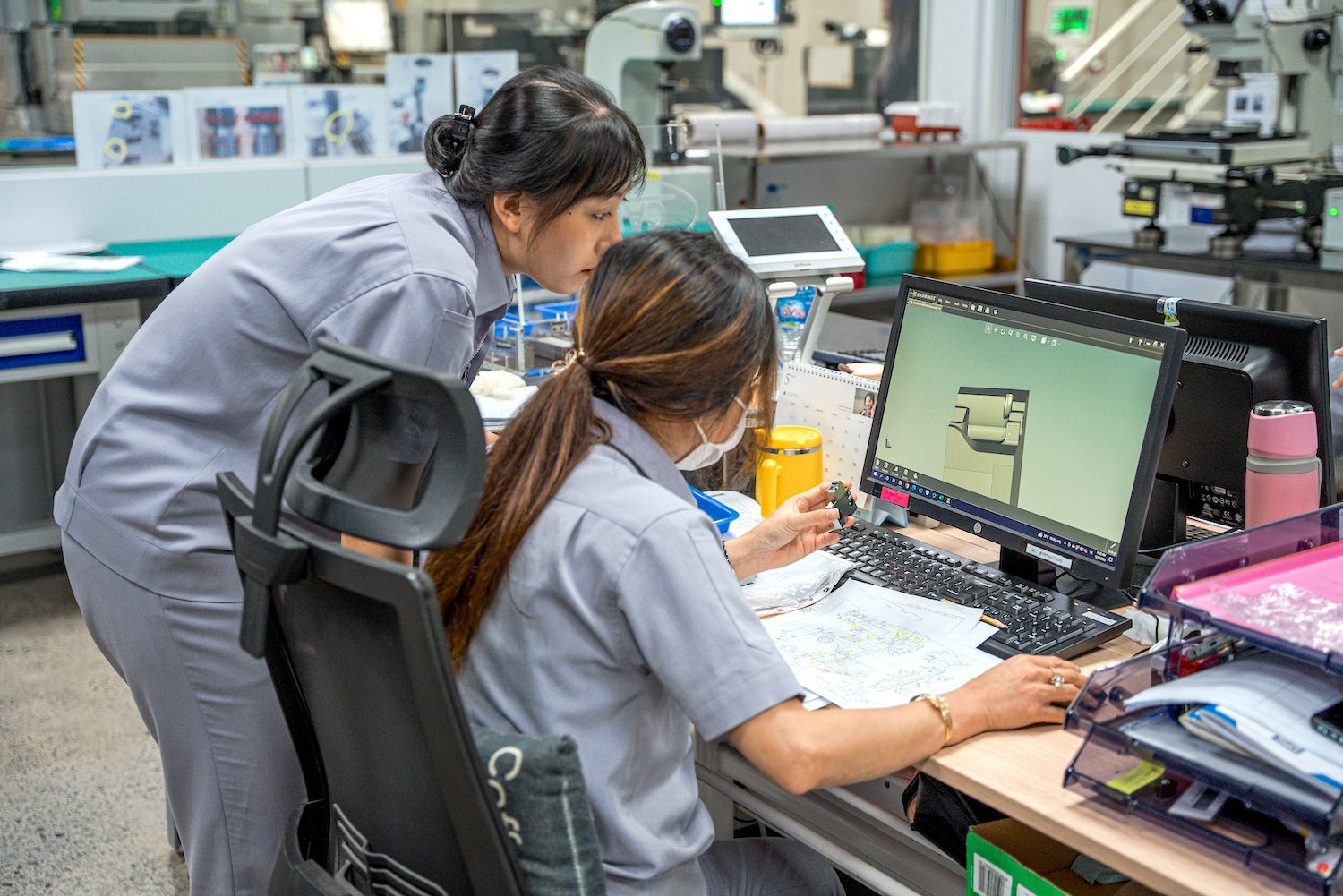
The meticulous attention to detail and precision demanded in achieving such tight tolerances rely on the use of these tools, ultimately driving up the overall manufacturing cost.
Cost-effective Alternatives for Precision Molds:
If you ever find yourself in a position not being able to spend $100,000 on one mold, try to opt for these more affordable options below.
3D Printing
Rapid advancements in 3D printing technology have made it a viable option for low-volume production and prototyping. This offers quick turnaround times and allows for design iterations at a fraction of the cost compared to traditional injection molds.
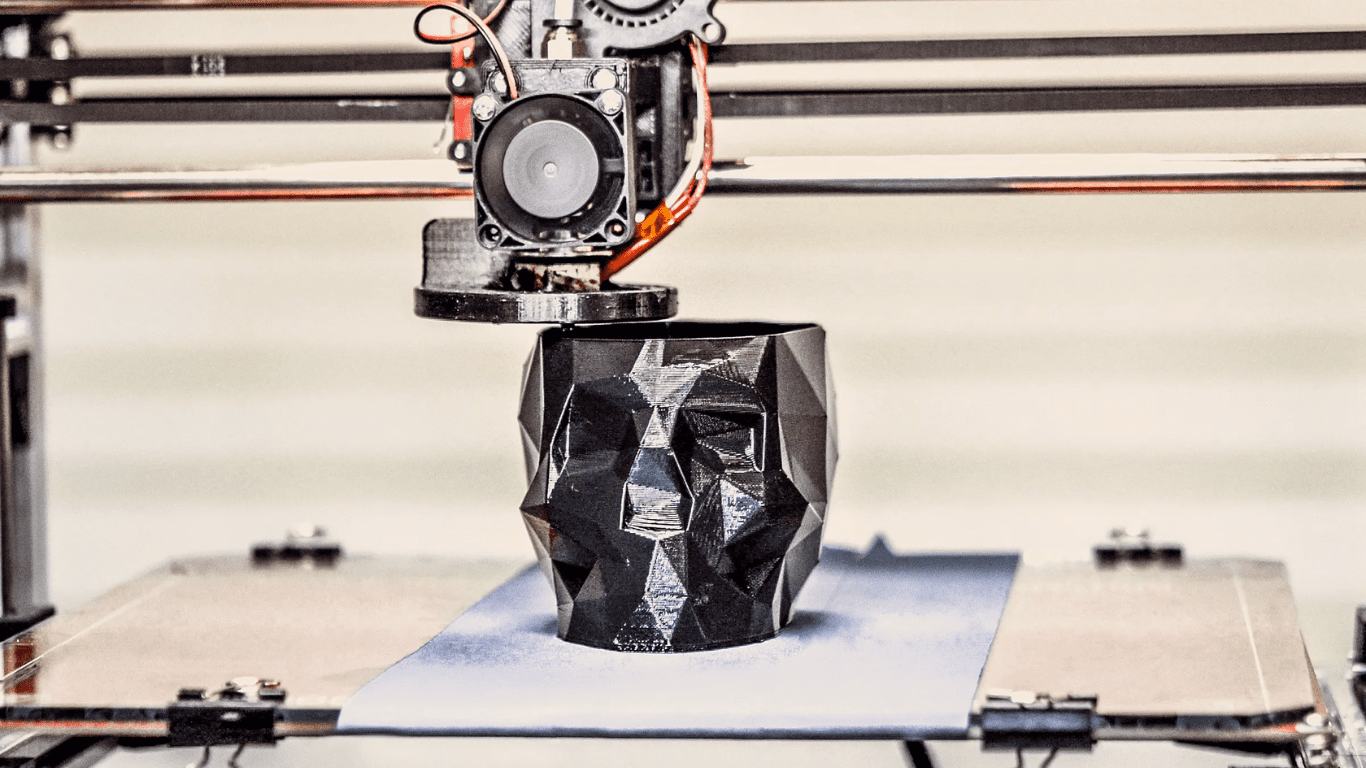
However, there are still evident drawbacks to alternating to 3D printing.
Firstly, 3D printing is generally slower than injection molding, especially for complex or large-scale objects. Material limitations are also a factor, as injection molding offers a wider range of materials compared to 3D printing.
Additionally, injection-molded parts tend to have smoother surface finishes, while 3D-printed parts may exhibit visible layer lines or imperfections. Lastly, although 3D printing allows for design freedom, certain features may require additional support or modifications, unlike injection molding which offers more flexibility.
Soft Tooling
Soft tooling, also known as silicone molds or urethane casting, is a cost-effective solution for small-scale production runs. Soft tooling can still provide functional prototypes or limited production quantities without the high upfront costs.
While it offers certain advantages, this methodology also has drawbacks when compared to traditional injection molding, like shorter lifespan and is more prone to wear and degradation compared to hardened steel molds. It is best suited for low-volume runs or prototyping rather than long-term or large-scale manufacturing.
Soft tooling, often made from materials like aluminum, epoxy, or silicone, may not be compatible with all materials or production requirements. It can result in longer cycle times due to slower cooling times, impacting overall production efficiency. Soft tooling may also lead to reduced dimensional accuracy and surface finish when compared to injection molding. Additionally, it can be more expensive per part due to frequent mold replacements, lower production efficiency, and additional post-processing needs.
Metal stamping
This is a cost-effective alternative to injection molding, particularly for high-volume production runs. The process involves the use of a die to shape and form metal sheets into desired components. It offers several advantages, including fast production cycles and high repeatability. Metal stamping is also suitable for applications that require tight tolerances. The process can handle a wide range of materials, including steel, aluminum, and copper.
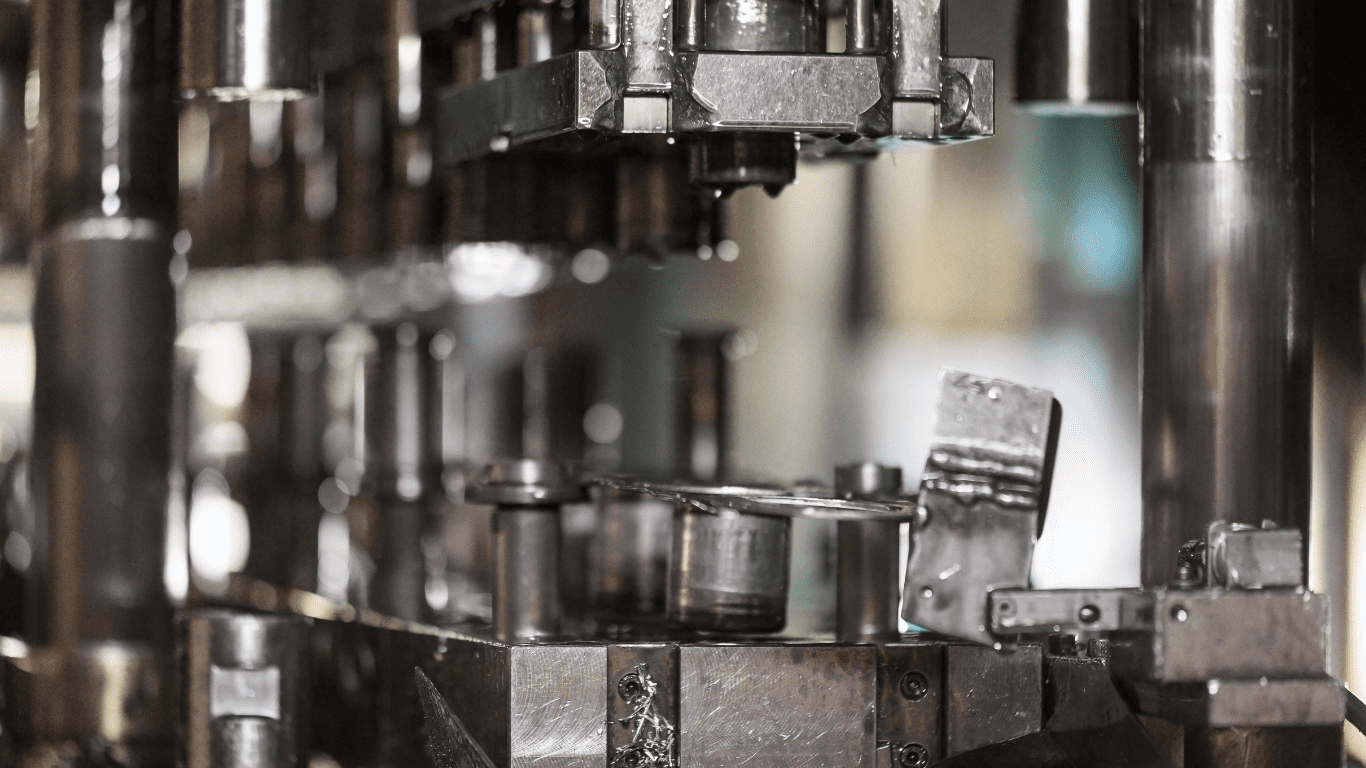
However, metal stamping does have some drawbacks. One limitation is its difficulty in producing complex shapes and designs, so the process is better suited for parts with simpler geometries. Additionally, the initial tooling costs for metal stamping can be higher compared to other manufacturing methods. This may make it less suitable for small production runs or prototypes, where the upfront investment may not be justified.
Die casting
Like metal stamping, die-casting is a popular alternative to injection molding due to its cost advantages and production efficiency. The process involves injecting molten metal into a mold cavity to create the desired shape. Die casting offers excellent dimensional accuracy and high production efficiency, making it suitable for large-scale manufacturing projects. It is capable of producing parts with complex shapes and thin walls. Die casting also provides flexibility in material selection.
However, die casting may not offer the same level of precision and tight tolerances as injection molding. The process is more prone to dimensional variations and may require additional post-processing steps to achieve the desired accuracy.
Factors to Consider Whilst Choosing Your Molding Partner
The search for a reliable manufacturer can be excruciating in this day and age where everyone is trying to grab your attention and bombard you with ads. Try to keep a few of these factors in mind when you look for your potential molding partner, and this can save you a lot of stress and a lot of $$$.
Expertise and Experience
When searching for a trustworthy partner in injection molding, it is crucial to find a company with a proven track record. Their expertise in mold design, material selection, and production efficiency will ensure ideal results.
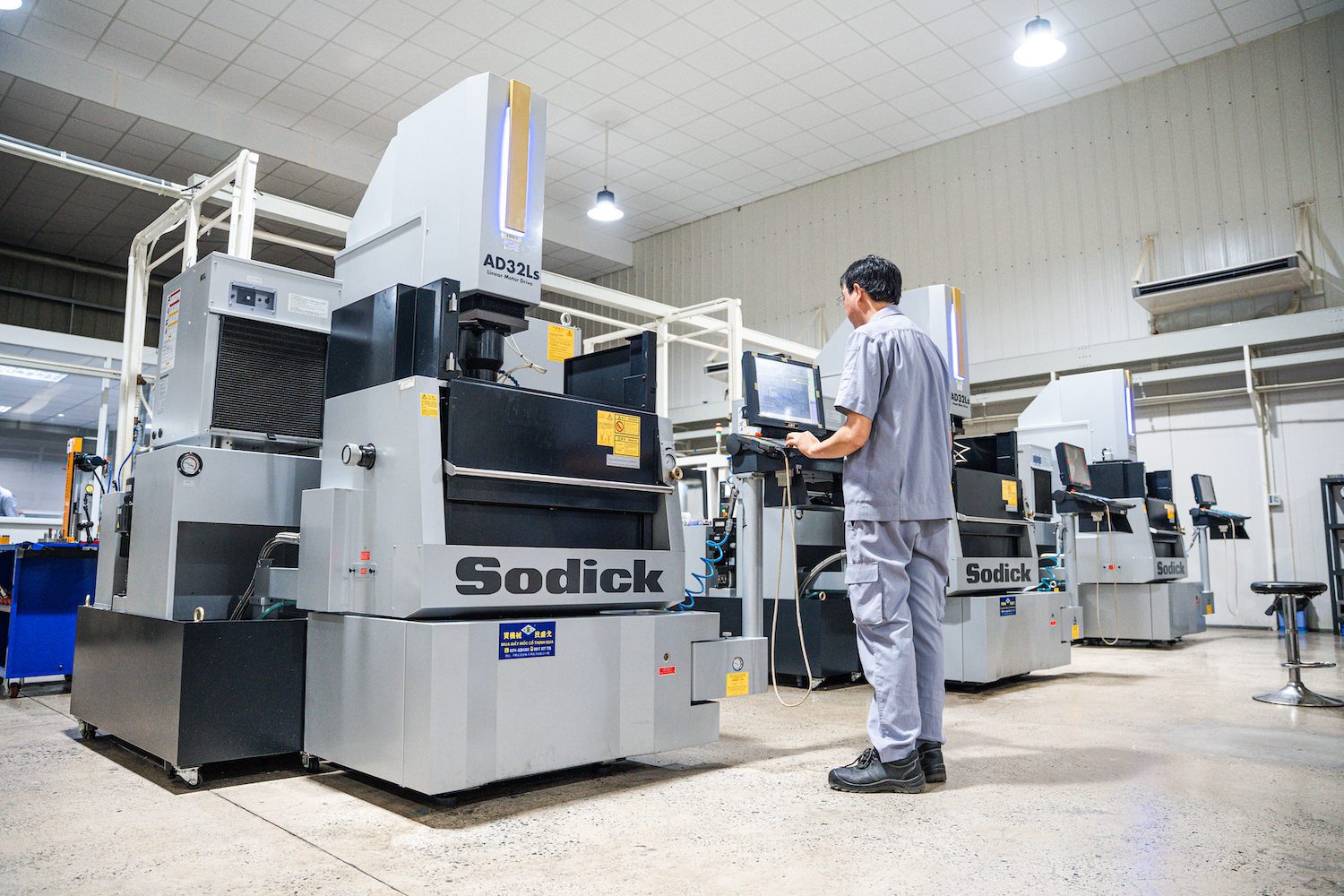
Quality Control
A reliable molding partner should have robust quality control measures in place to ensure consistent part quality. Certifications like ISO 9001 might demonstrate their commitment to quality management systems.
Cost-efficiency
Evaluate the partner’s pricing structure, including mold design and production costs, to ensure they align with your budget and offer affordable rates.
When In Doubt, Turn To CAM Resources!
At CAM Resources, we understand the challenges businesses face when it comes to looking for a trustworthy injection mold manufacturer. With our extensive experience and expertise in injection molding, we strive to provide cost-effective solutions without compromising on quality. Whether you require high-volume production or low-volume prototyping, our team is committed to delivering exceptional results.
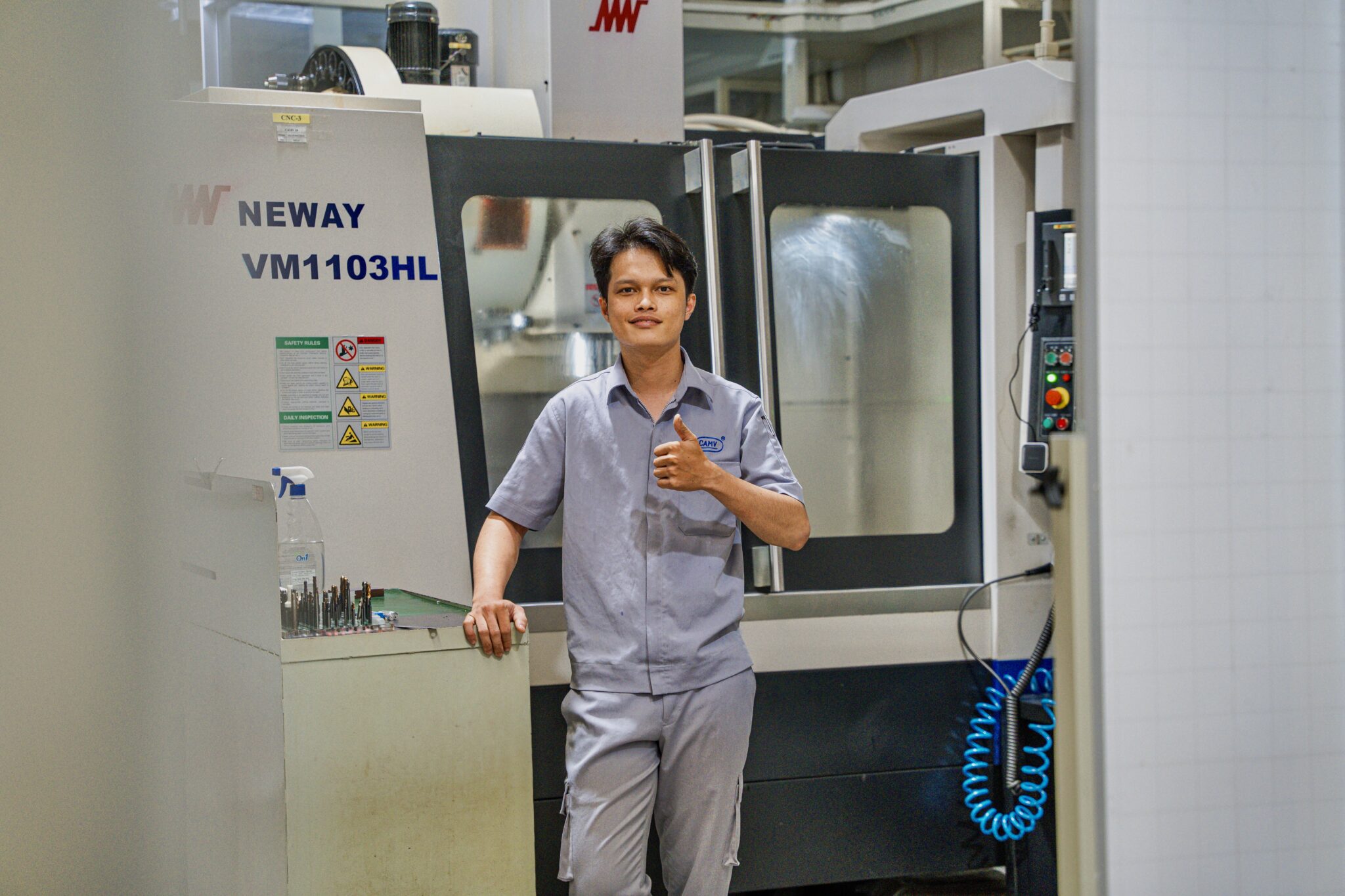
CAM Resources can truly be the reliable molding partner that you are looking for, offering the best of both worlds: affordable pricing and top-notch quality. Contact us anytime to discuss your product design and receive a personalized quote.