If you’re looking for a reliable and efficient way to mass-produce plastic parts, injection molding should be at the top of your list. Whether you’re a seasoned industry professional or just starting out, this blog will provide you with all the information you need to know about injection molding machines.
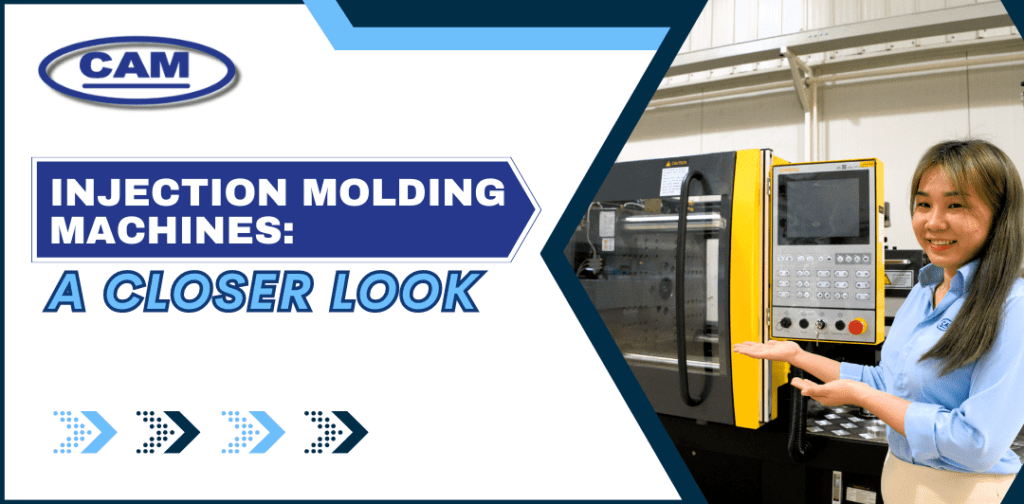
Injection molding machines are widely used for manufacturing plastic products for various industries. They can produce complex shapes as per the desired industry specifications with high precision and at a low cost. It can also use different types of plastics and additives to create products with different properties and colors. Injection molding machines are used for making products such as packaging, automotive parts, electronics, medical devices, and a wide range of household items.
Buckle up, because we’re giving you a guide through the different types of injection molding machines, their benefits, applications, and more.
The Injection Molding Process
Now, let’s take a look at how injection molding machines are operated. Basically, the injection molding process produces identical plastic parts by injecting molten material into a mold. This process consists of four main stages: clamping, injection, cooling and ejection.
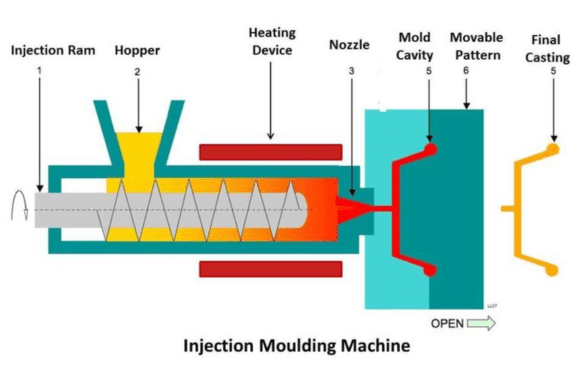
1. Clamping
The first stage is to clamp the two halves of the mold together using a hydraulic or mechanical force. The mold is usually made of steel or aluminum and has cavities that match the shape of the desired part. The mold also has channels for injecting molten plastic and vents for releasing air and excess plastic.
2. Injection
The second stage is to inject molten plastic into the mold cavity using a screw or plunger. The plastic is heated in a barrel until it reaches a fluid state and then forced into the mold under high pressure. The injection time and speed depend on the size and shape of the part and the type of plastic used.
3. Cooling
The third stage is to cool the plastic part inside the mold until it solidifies. The cooling time and rate depend on the thickness and geometry of the part and the thermal properties of the plastic and the mold. During cooling, the plastic shrinks and conforms to the shape of the mold cavity.
4. Ejection
The final stage of the injection molding process is to eject the plastic part from the mold using ejector pins or air blasts. The part is then removed from the mold and inspected for quality and defects.
Factors Affecting The Injection Molding Process
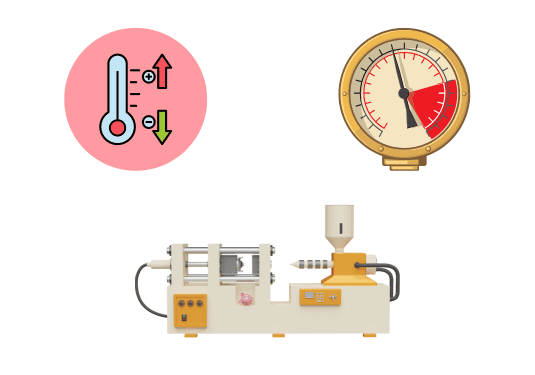
The injection molding process relies heavily on temperature and pressure control. Temperature control involves heating and cooling both the plastic and the mold. The ideal plastic temperature should allow easy flow into the mold cavity without degradation or flashing. The mold temperature should allow fast cooling and solidification of the part without warping or cracking.
Pressure control involves applying and releasing pressure during different stages of the injection molding process. The injection pressure should fully fill the mold cavity without causing excessive stress or distortion. The packing pressure should be maintained until the gate freezes to prevent sink marks or voids. Gradually releasing the holding pressure allows for uniform shrinkage and avoids residual stress.
To put it simply put, the injection molding process is complex and versatile and can produce high-quality plastic parts of various shapes and sizes. By understanding and controlling temperature and pressure during injection molding, injection molders can improve their product performance and reduce their production costs.
Types of Injection Molding Machines
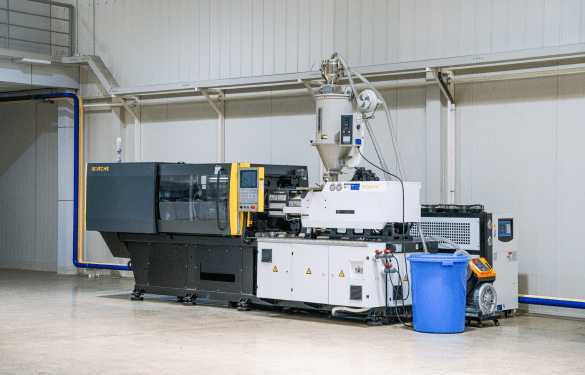
With you getting a grasp of the injection molding process, let’s find out more about the different types of injection molding machines.
Injection molding machines can be categorized based on the type of driving system. This system is the mechanism that transmits power from the motor to the injection unit and the mold clamping unit. There are four main types of driving systems based on their design and operation:
1. Hydraulic
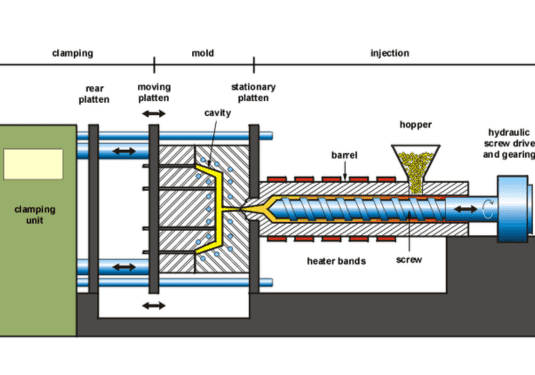
Hydraulic injection molding machines use a hydraulic pump to generate the pressure and force needed for injection and clamping. Hydraulic machines are the most common type of injection molding machines, as they offer high clamping force, large shot size, and flexibility in controlling injection speed and pressure. However, hydraulic machines also have some disadvantages, such as high energy consumption, noise, heat generation, and potential oil leakage.
2. Mechanical
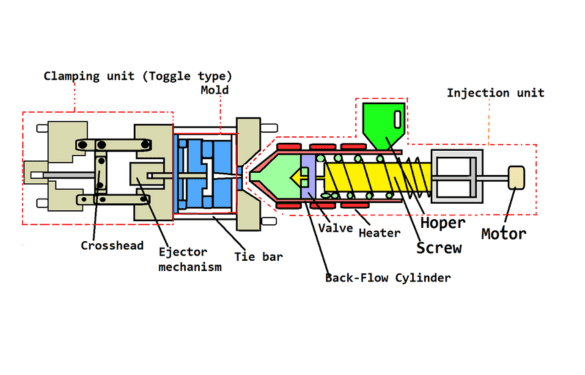
Mechanical injection molding machines use a toggle mechanism to generate the clamping force. Mechanical machines are simpler and cheaper than hydraulic machines, as they have fewer components and require less maintenance. Mechanical machines also have faster cycle times and lower energy consumption than hydraulic machines. However, mechanical machines have limited clamping force and shot size, and they cannot control the injection speed and pressure precisely.
3. Electric
Electric injection molding machines use servo motors to drive the injection and clamping units. Electric machines are more precise, efficient, and clean than hydraulic or mechanical machines, as they can control the injection speed and pressure accurately and eliminate the need for oil. Electric machines also have lower noise and heat generation than hydraulic or mechanical machines. However, electric machines are more expensive than hydraulic or mechanical machines, and they have a lower clamping force and shot size.
4. Hybrid
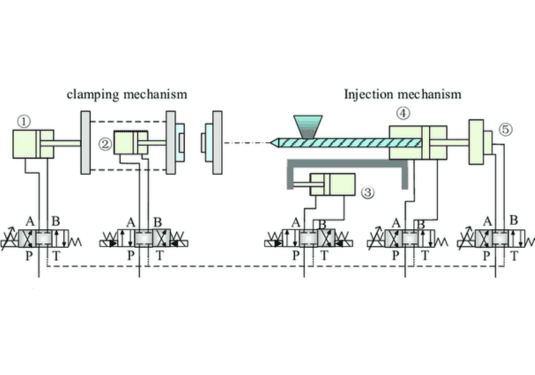
Hybrid injection molding machines combine the advantages of hydraulic and electric systems, offering high clamping force and shot size, as well as precise control over injection speed and pressure, with lower energy consumption and noise. However, it is more complex and costly than hydraulic or electric machines and still generates some heat and oil leakage.
So basically, injection molding machines can be categorized based on their driving systems, which include hydraulic, mechanical, electric, and hybrid systems. Each system has its own advantages and disadvantages. Choosing the right type of machine depends on the specific needs of the product and the production process. Manufacturers should carefully evaluate the trade-offs between cost, performance, maintenance, and environmental impact when selecting an injection molding machine.
Advantages of Injection Molding Machines
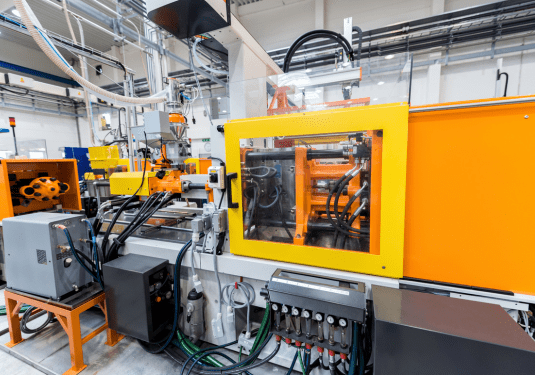
Now that the different types of injection molding machines have been explained to you, a question arises: Why should you use injection molding machines?
If you are looking for a manufacturing process that can produce large quantities of plastic parts with high precision and low cost, you might want to consider injection molding. Plastic injection molding machines are devices that have several advantages over other methods of plastic production. Here are some of the main benefits of injection molding machines:
Higher Production Rates
Injection molding machines can produce hundreds or thousands of parts per hour, depending on the size and complexity of the mold. This makes them ideal for mass production of plastic products, such as toys, containers, medical devices, and automotive parts. Injection molding machines can also run continuously, 24 hours a day, seven days a week, without interruption or downtime.
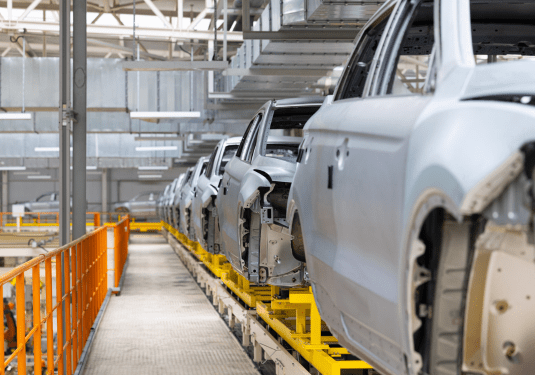
Low Labor Costs
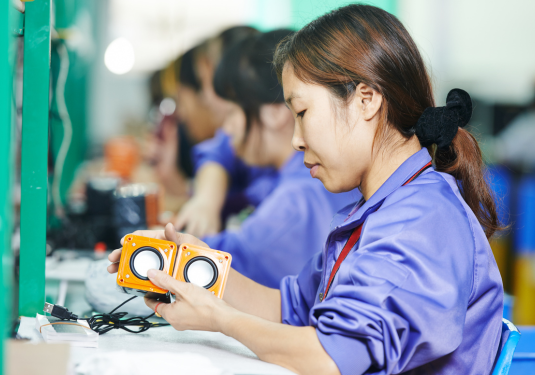
Injection molding machines are highly automated and require minimal human intervention. The operator only needs to load the raw material, monitor the machine parameters, and unload the finished products. The rest of the process is controlled by the machine itself, which reduces the need for skilled workers and lowers the labor costs.
Consistent Product Quality
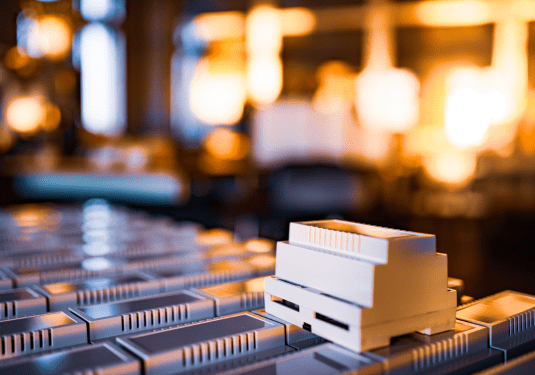
Injection molding machines can produce parts with high accuracy and consistency, as they follow the exact specifications of the mold. The parts have uniform dimensions, shape, and weight, and they have minimal defects or variations. Injection molding machines can also maintain the quality of the plastic material, as they prevent contamination and degradation during the heating and cooling cycles.
So there’s that, injection molding machines provide a cost-effective and efficient method for producing large quantities of plastic parts with high precision and consistency. If you are looking to manufacture plastic products on a large scale, injection molding is definitely worth considering.
Common Applications of Injection Molding Machines
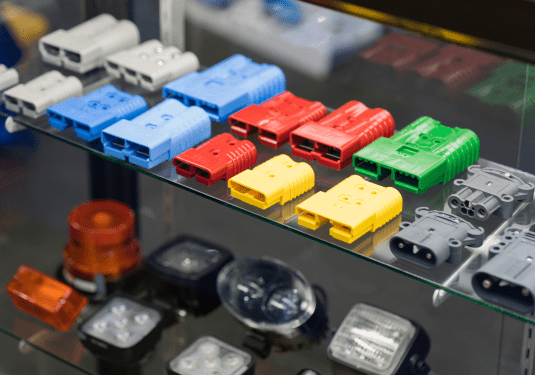
Generally, injection molding machines are widely used in different industries because they can produce complex and precise shapes with high efficiency and low cost. Some of the common applications of injection molding machines are:
1. Automotive
Many different automotive components, including bumpers, dashboards, door panels, engine covers, etc., are made with the use of injection molding machines. Additionally, plastic parts for electric car components like connections and battery housing can be produced by injection molding machines.
2. Medical
Syringes, catheters, implants, surgical instruments, and other pieces of medical technology are produced by injection molding machines. The use of injection molding machines may guarantee the products’ high quality and sterility as well as lower their risk of contamination and infection.
3. Packaging
Injection molding machines are also used to make plastic containers and bottles for food, beverages, cosmetics, pharmaceuticals, etc. Injection molding machines can produce different shapes and sizes of packaging with various features, such as caps, labels, handles, etc.
4. Consumer Electronics
Plastic cases and components for smartphones, tablets, laptop computers, cameras, and other electronic devices are manufactured using injection molding equipment. For touchscreens and displays, injection molding machines can also create flexible and transparent plastic materials.
In summary, injection molding machines have a wide range of applications in different industries. From automotive parts to medical devices, from packaging to consumer electronics, and even more, injection molding machines play an important role in creating the products we use every day.
Before you go
We have reached the end of this blog post, where we have covered everything you need to know about injection molding machines. Injection molding machines are essential for modern manufacturing, as they can produce complex and precise plastic parts in large quantities with minimal waste.
But have you ever wondered where plastic products are shaped? It happens in the molding cavity, a key part of the injection molding process. Mold manufacturers specialize in making these molds. They use advanced technology and engineering to create molds that can handle the high pressures and temperatures of molding while producing high-quality products.
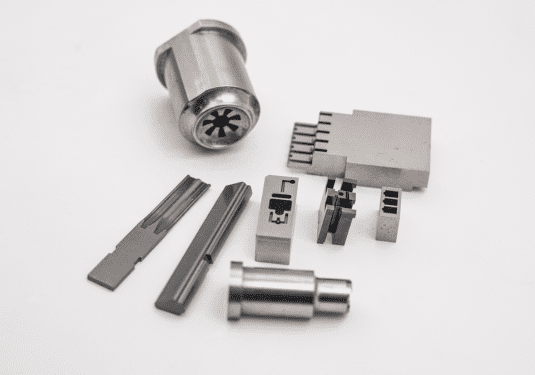
If you are looking for a reliable and experienced partner for your injection molding needs, look no further than CAM Resources. CAM Resources’ Vietnam factory CAMV is a leading provider of services relating to plastic injection molding machine. We also manufacture high-quality injection molding machine components, such as jigs, fixtures, die sets, mold sets, and mold and die components. We are confident in our ability to deliver your orders with near-zero accuracy and assured on-time delivery.
CAM Resources is committed to delivering the best solutions for your injection molding projects. Contact us today to find out how we can help you achieve your goals with injection molding machines.
It never crossed my mind that people rely on injection molding to create catheters and many surgical tools as well. That being said, it’s time for my cousin to contact a manufacturer as soon as possible. As someone who works at a clinic, he always deals with the shortage of medical equipment which is something he’s had enough of.