From dull metal sheets to well-crafted cars and planes, manufacturers count on this reliable technique. Let’s break down metal stamping, the process that gives shape and purpose to metal.
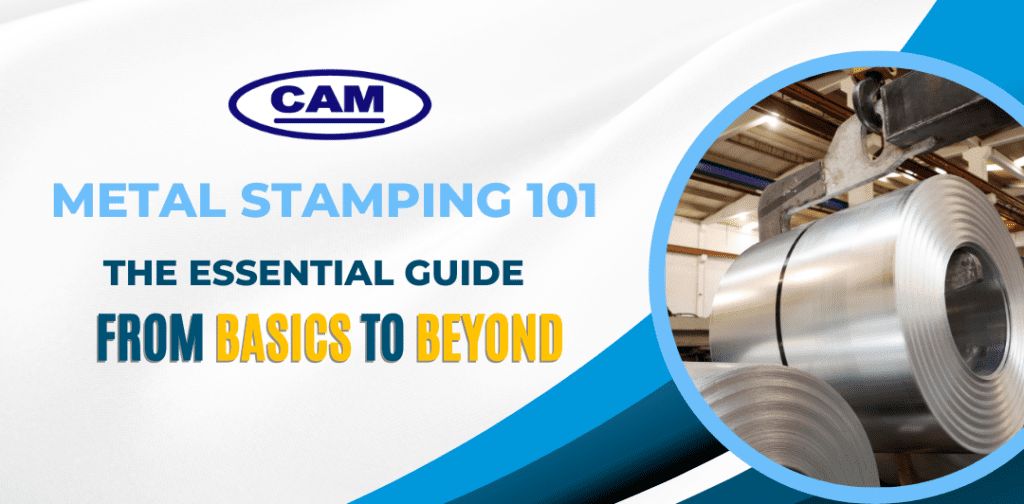
Would you believe that we are in a world where everyday objects, from your smartphone casing to the intricate components of a car engine, owe their existence to the art and science of metal stamping? In this era of modern manufacturing, metal stamping does not just emerge as a technique; it stands out as a transformative force that shapes multiple industries.
Whether it’s shaping the aerodynamic curves of automotive panels or crafting the delicate intricacies of electronic components, metal stamping acts as the invisible hand, sculpting the tangible elements of our daily lives. So let’s delve into the metal stamping from A to Z.
Understanding Metal Stamping
Metal stamping is a manufacturing technique that transforms flat metal sheets or coils into precisely shaped components through a series of mechanical processes. This method involves the use of a stamping press and customized dies, where flat sheet metal, in either coil or blank form, is placed. The metal is then formed into the desired shape using a tool and die surface.
Depending on the requirement, various stamping techniques such as punching, blanking, bending, coining, embossing, and flanging are employed in stamping to shape the metal. Below is a diagrammatic representation of how a typical metal stamping works:
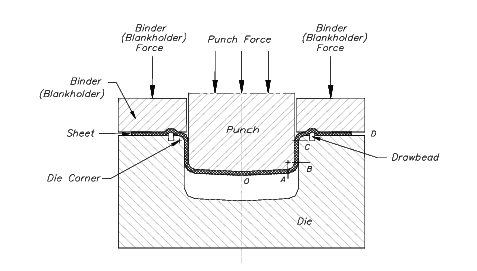
The main parts involved are:
- The binder (blankholder): to hold the blank in place to prevent it from wrinkling or buckling.
- Punch: The upper part of the die set that cuts or forms the metal blank.
- Die cavity: The lower part of the die set that defines the final shape of the stamped part.
- Sheet metal blank: The flat sheet of metal that is being stamped into the desired shape.
When it comes to the working principle, a blank is placed between the upper and lower dies. The binder secures the blank, and a punch will press it into the die cavity, shaping the metal. After retracting the punch, the finished part is ejected. The binder force is an important parameter in metal sheet stamping; a force too low will cause wrinkling, whilst a force too high might lead to improper flow and deformation.
MAKING DIES FOR METAL STAMPING
The process begins with designing the tooling, using CAD/CAM engineering technology. The precision of these designs is crucial to ensure that each punch and bend maintains proper clearance, to ensure optimal part quality. The tool’s 3D model can be complex, containing hundreds of parts, making the design process intricate and time-consuming. Once the tool’s design is established, manufacturers utilize machining, grinding, wire EDM, and other manufacturing services to produce the tool. This tool is then used in the stamping press to create the desired shapes from sheet metal.
The overall process is fundamental to metal forming and manufacturing in various industries, including automotive, aerospace, electronics, and appliances, to produce parts such as brackets, clips, connectors, and more. It offers advantages like high production speed, cost-effectiveness for large production runs, and the ability to maintain tight tolerances in part dimensions.
Precision in Every Cut: The Process Unveiled
Metal stamping is a versatile and powerful manufacturing technique that encompasses a diverse range of processes beyond just blanking. Each process serves a specific purpose and works in tandem to achieve the desired final form of the metal component. Below are some of the common processes:
- Blanking: This process will separate a desired shape from a metal sheet using a die set. The punch cuts along the outline of the desired shape, while the die provides support and prevents tearing.
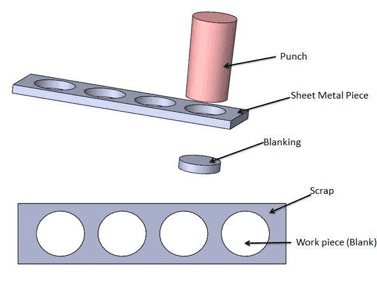
- Punching: In metal stamping, punching refers to the process of using a punch and die set to cut, pierce, or shape a metal workpiece. The punch is a tool that applies force to the metal, while the die is a counterpart tool that provides the desired shape or opening. Punching is a common technique in metal stamping used for creating holes, notches, or other geometric features in the metal material.
- Bending: Bending is the process of deforming a metal workpiece, typically a sheet or strip, to achieve a specific angle or shape. This is accomplished by applying force to the material, causing it to bend around a predetermined axis. Bending is a fundamental operation in metal forming, allowing manufacturers to create various geometries and contours in stamped metal components.
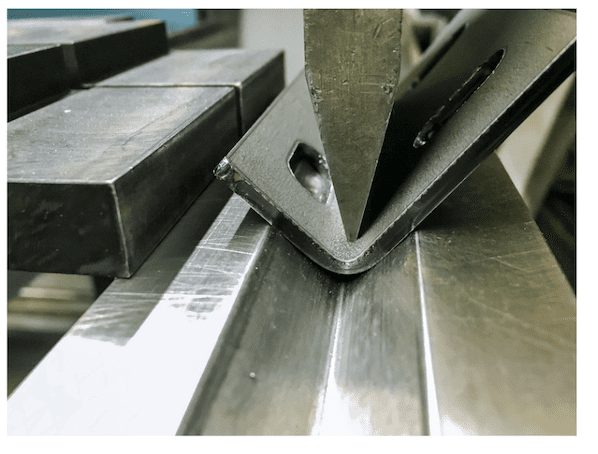
- Coining: This process entails positioning the material between a die and a press or punch. The material undergoes extreme pressure during the press stroke, resulting in the creation of fine features and tight tolerances on the surfaces of the produced parts.
- Assembly: Multiple stamped components can be seamlessly assembled, utilizing welding, fasteners, or other joining techniques to create the final product.
These are just a few of the many processes that orchestrate the metamorphosis of metal in stamping. Each operation contributes to the final composition, and the precision achieved in this intricate dance ensures the reliability and quality of the end product.
Types Of Metal Stamping
Various techniques are employed in different types of metal stamping processes to produce finished parts that meet high-quality standards. The three primary categories of metal stamping are Progressive Die Stamping, Deep Draw Stamping, and Fourslide Stamping.
1. Progressive Die Stamping
Progressive die stamping is a metalworking process designed for the efficient and rapid production of multiple parts. This method, based on a variation of the general metal and die stamping process, is particularly well-suited for high-volume manufacturing of intricate components. In the long-run progressive stamping process, sheets of metal are cut and formed using a specialized stamping die. The procedure involves a series of distinct workstations, with each station within the press being dedicated to a specific function (such as forming, punching, bending, or cutting the metal). This streamlined approach allows for the creation of numerous intricate parts in a cost-effective and time-efficient manner.
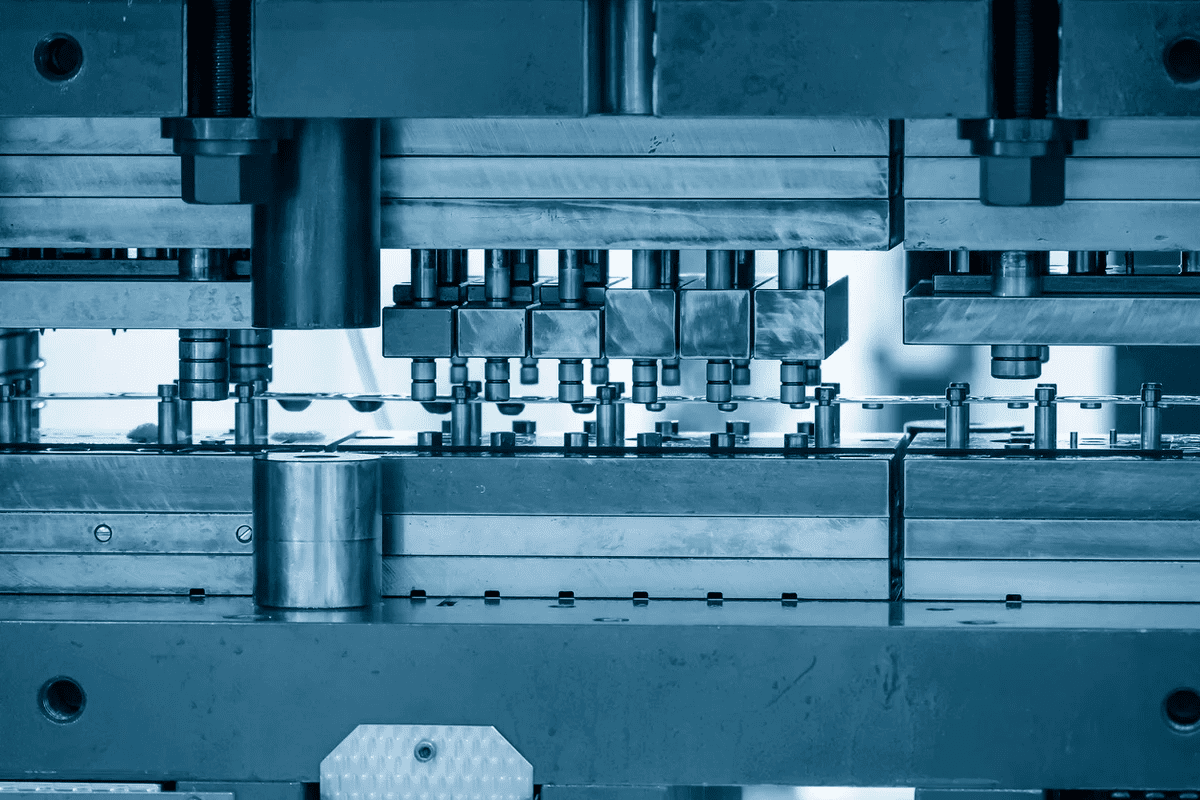
2. Fourslide Stamping
Fourslide stamping is a metalworking process designed to streamline the production of complex parts. This method employs four tools, each responsible for bending the metal into the required shape simultaneously. Unlike progressive stamping, which excels in high-volume uniformity, fourslide stamping allows for the efficient production of complex parts in smaller quantities, making it adaptable to different manufacturing needs.
3. Deep Draw Stamping
Deep drawing is a metal forming process that uses a punch and die to draw a sheet metal blank into a desired shape. The depth of the drawn part is typically greater than its diameter..It is commonly applied in industries such as Automotive and Aerospace, where components with sweeping and deep shapes are prevalent.
One notable advantage of deep drawing is its efficiency in terms of raw material usage. This process tends to require less material compared to other stamping techniques, contributing to its cost-effectiveness and resource conservation.
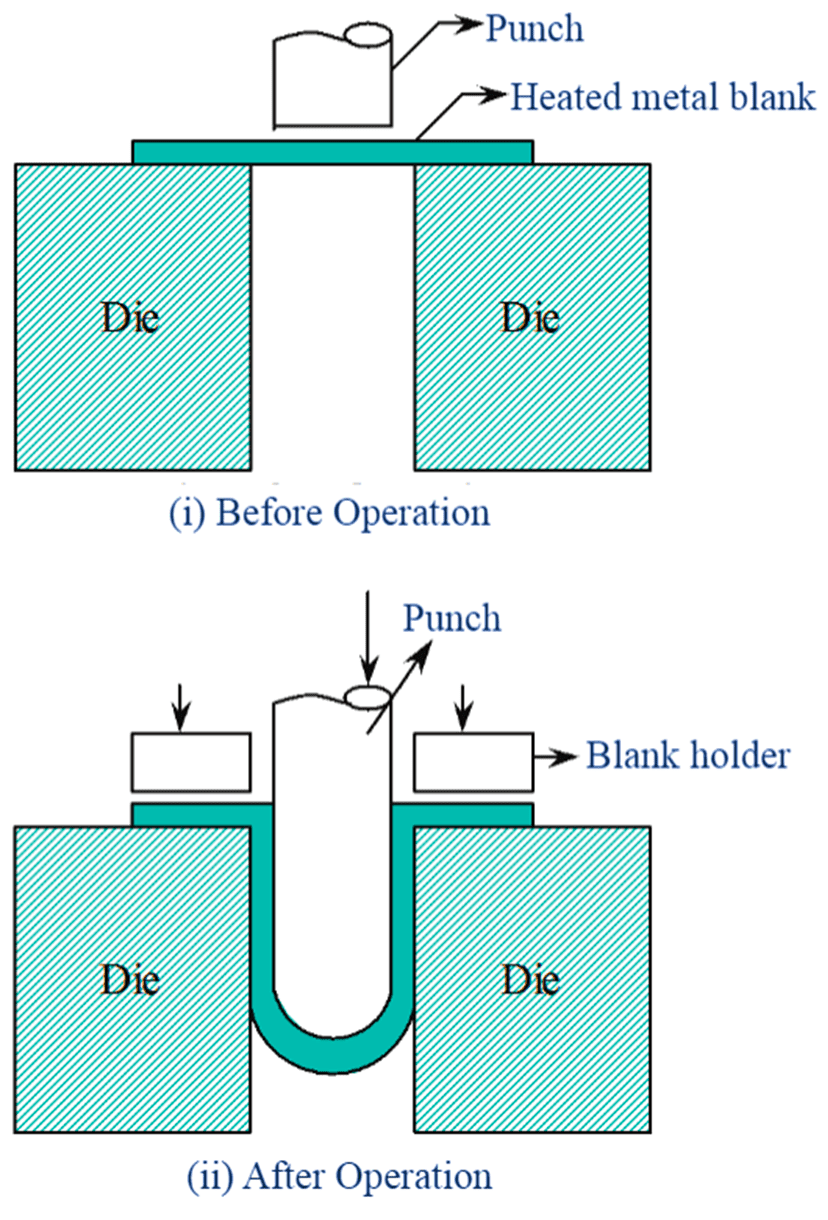
Applications Across Industries
1. Automotive:
Metal stamping has had a major impact on how cars are made. It’s a powerful technique that uses a mold (die) and a press to shape sheets of metal into precise parts. This makes it perfect for manufacturing all sorts of things in cars, from the outside body panels to the inside brackets and chassis pieces. Since it’s so fast and versatile, metal stamping has become a key part of making cars efficient and beautiful.
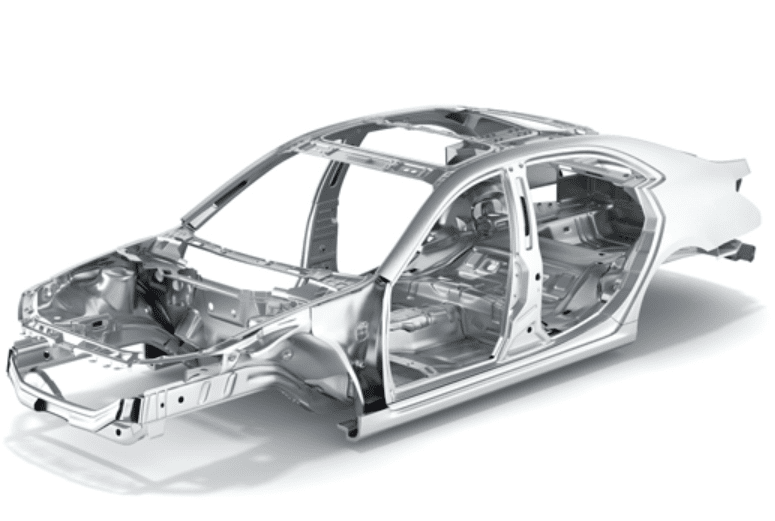
2. Electronics:
Within the fast-growing electronics industry, the demand for precise, intricate, and uniform parts is of paramount importance, requiring manufacturers to remain abreast of the sector’s dynamic landscape to ensure success. The utilization of advanced metal stamping techniques has revolutionized the manufacturing process, enabling the rapid, accurate, and consistent production of even the smallest components.
3. Aerospace:
In the high-stakes world of aerospace, where every component plays a crucial role in ensuring safety and performance, metal stamping takes center stage. This versatile manufacturing technique helps craft intricate and uniform parts with remarkable precision, making it a cornerstone of building modern aircrafts and spacecrafts. A testament to the important role of metal stamping can be found in the hearts of all airplanes, as their engines have parts that went through highly sophisticated metal stamping procedures to ensure strict precision requirements.
4. Appliances:
Metal stamping is a widely used manufacturing process in the production of various home appliances. From kitchenware to household gadgets, metal stamping plays a crucial role in shaping and forming the components of these appliances. This technique allows for the mass production of precise and consistent parts, making it an efficient and cost-effective method for creating home appliances.
CAM Resources: Your Partner For Metal Stamping Success
Metal stamping stands as a cornerstone in manufacturing, offering a versatile and efficient solution to producing intricate metal components. Throughout this exploration, we’ve delved into the fundamental processes and diverse applications that define the landscape of metal stamping.
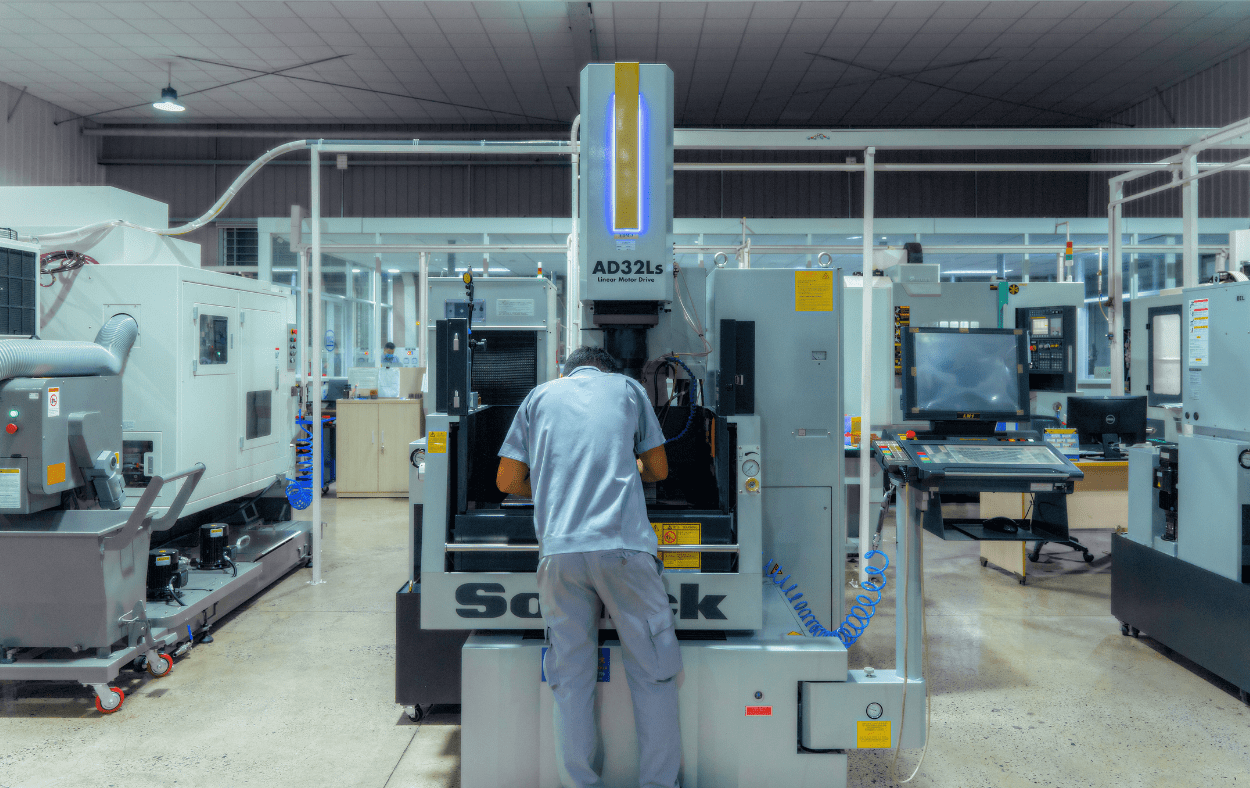
In today’s fiercely competitive manufacturing landscape, you need a partner who can deliver high-quality, precision metal stamping dies on time and within budget. CAM Resources is your partner, with years of experience in serving the metal stamping industry, we are always well-equipped with the best talents and the latest machining technology. Check out our latest product capabilities by clicking here.
Contact us today to learn more about our services and how we can help you achieve your manufacturing goals.