Precision tooling is crucial in various industries when making precisely shaped products. The materials chosen can significantly impact the quality and efficiency of both the molds and the final product. Hence, it is imperative that manufacturers make good decisions based on the application specifications. This blog will serve as an overview of the available options, their pros and cons, and eventually help you make the right choice for you!
The world is all about making smart choices that suit you and serve your purpose. Whether you are choosing a car or a job among the many available options, careful consideration and weighing of factors, along with understanding the consequences, will lead to informed and effective decision-making. The same principle applies to precision tooling material selection as well, saving the day with desired outcomes.
Precision tooling and mold manufacturing play a role, in industries, such as automotive, aerospace, electronics, and medical. The ultimate quality and performance of the end product greatly depend on the materials chosen for the mold manufacturing process. It is crucial to select the material that ensures functionality, durability, and cost-effectiveness.
In this guide, we will explore the factors to consider when selecting materials for precision mold manufacturing. We will delve into the types of materials, their specific properties, and their suitability for various applications. thus helping manufacturers and machinists improve production by promoting an understanding of material selection intricacies. Let’s dive in!
Understanding the Role of Precision Tooling:
Precision tooling comprises custom precision mold & die sets, custom precision mold components, die components, Jigs, and fixtures. They play a crucial role in manufacturing for several reasons stated below:
Quality and Enhanced Efficiency
Precision tooling ensures that the products being manufactured meet the required specifications and tolerances, reducing production time and costs. They help maintain consistency and accuracy in the manufacturing process, resulting in high-quality products that withstand wear and tear and increase the lifespan of the final products.
By ensuring accurate cuts and measurements, manufacturers can optimize the use of raw materials, minimizing waste and reducing rework or scrap eventually leading to cost savings.
Diversity and Versatility:
Precision tooling allows manufacturers to work with a wide range of materials, including metals, plastics, and composites. This versatility enables manufacturers to produce diverse products and meet the demands of various industries.
Innovation and Customization:
Precision tooling enables manufacturers to create complex and intricate designs. It allows for the production of customized products that meet specific customer requirements, fostering innovation and enabling manufacturers to stay competitive in the market.
Why material selection is critical for your precision Tooling?
One must note that there’s no one-size-fits-all approach when it comes to choosing the best material for your mold. Instead, the most appropriate material depends on your specific requirements and objectives. Let’s run through why mold manufacturers and technicians must take material selection for precision tooling seriously:
1. Ensuring Wear Resistance for Longevity
Precision tooling is a critical element of many industries, and it is often subjected to high levels of wear and tear during use. As such, selecting a material with excellent wear resistance is crucial to ensure that the tools last longer and require less frequent replacement, leading to increased efficiency and cost savings.
Carbide and ceramic materials are two of the most popular materials used in precision tooling due to their exceptional wear resistance properties. Carbide is known for its high hardness, strength, and toughness, making it suitable for use in high-speed machining and heavy-duty applications. On the other hand, ceramic materials are known for their excellent wear and corrosion resistance, high-temperature stability, and low thermal expansion coefficient, making them ideal for use in high-precision and high-temperature applications.
By choosing the appropriate material with high wear resistance, businesses can achieve optimal performance and longevity of their precision tools, leading to increased productivity and profitability.
2. Guaranteeing Dimensional Stability
Precision tooling must maintain its dimensional accuracy over time, even under changing temperature and humidity conditions. Therefore, selecting a material with excellent dimensional stability is critical to ensuring that the tooling maintains its accuracy and consistency throughout its lifespan.
Steel and titanium are two materials that are known for their exceptional dimensional stability properties, making them ideal for use in precision tooling. Steel is often preferred for its high strength, durability, and resistance to wear and tear, making it suitable for use in high-volume production environments. Titanium, on the other hand, is known for its low density, high strength-to-weight ratio, and excellent corrosion resistance, making it ideal for use in aerospace and medical applications.
With a deep understanding of choosing a material with good dimensional stability, businesses can ensure that their precision tooling maintains consistent accuracy and reliability, leading to improved quality control and customer satisfaction.
3. Assuring Machinability
The material used in precision tooling must be easily machinable, as the tools themselves are often manufactured using precision machining techniques. Some of the most used and dominant machines for precision molding that materials must be considered to be fit are CNC, EDM, and Wire-cut machines. Hence, selecting a material that is easy to machine is critical to reducing manufacturing costs and lead times while ensuring the required level of precision.
Both aluminum and steel are widely recognized for their outstanding machinability properties, making them ideal for use in precision tooling. Aluminum is a lightweight and highly versatile material that can be easily machined using standard machining techniques, making it ideal for use in high-volume production environments. Steel, on the other hand, is a durable and robust material that can be machined using a variety of techniques, including milling, drilling, and turning.
In summary, the careful selection of materials for precision molding, with a focus on ease of machinability, can have a significant impact on a business’s bottom line. Considering the dominant and widely used machines such as CNC, EDM, and Wire-cut machines can help businesses optimize their manufacturing processes and achieve their goals.
The top 5 raw materials for the ultimate tooling solutions
Different materials have unique properties that make them suitable for specific applications, and selecting the appropriate material is crucial to achieving optimal results. So, let’s dive into the world of precision tooling and molding and discover the benefits of these top raw materials!
1. Stainless Steel
Steel is a widely used material in various industries, including precision tooling and molding. It is an alloy made primarily of iron, carbon, and other elements such as manganese, silicon, and sulfur.
Steel is known for its exceptional strength, durability, and resistance to wear and tear, making it ideal for use in high-volume production environments. Therefore, it is one of the most commonly used in precision tooling. Furthermore, It can be machined using a variety of techniques, including milling, drilling, and turning, and is often preferred for its excellent dimensional stability properties. Steel comes in different grades and forms, each with unique properties that make them suitable for specific applications.
Overall, steel is a versatile and reliable material that has become a cornerstone of modern manufacturing which makes it a popular choice for precision tooling applications
2. Carbide
Carbide material, a composite of metal (typically tungsten or titanium) and carbon is widely used in precision tooling due to its exceptional hardness, durability, and resistance to wear and heat. With its hardness surpassing that of traditional tooling materials like steel, carbide tools maintain cutting edges for extended periods, delivering improved precision and reduced wear.
The outstanding wear resistance of carbide enables it to withstand high-speed machining and prolonged use, ensuring optimal performance in demanding precision tooling applications. Additionally, its high melting point grants carbide the ability to endure extreme temperatures without deformation or softening, guaranteeing consistent and reliable results.
The dimensional stability of carbide materials also allows for precise and accurate machining, even under heavy loads and high temperatures, crucial for achieving tight tolerances in precision tooling. Lastly, the versatility of carbide enables customization through various grades and compositions, catering to specific machining operations, materials, and cutting conditions.
Overall, carbide’s combination of hardness, wear resistance, heat resistance, precision, and versatility makes it the go-to material for precision tooling, offering unparalleled accuracy, durability, and performance.
3. Titanium
Titanium is a highly desirable material for precision tooling solutions, due to its exceptional strength, low density, and corrosion resistance properties. Its high strength-to-weight ratio makes it an ideal choice for creating strong yet lightweight tools, reducing operator fatigue, and enhancing productivity.
The remarkable resistance to corrosion ensures the longevity and reliability of titanium tools, making them suitable for use in harsh environments. Additionally, titanium’s ability to withstand high temperatures makes it an excellent choice for applications that require tools to maintain their structural integrity and cutting performance under extreme conditions.
Also, the biocompatibility of titanium also makes it suitable for medical and dental applications, where sterile and non-reactive tools are essential. The excellent machinability of titanium allows for precise shaping and intricate designs, ensuring accuracy in machining operations. The durability and wear resistance of titanium result in longer tool lifespan, reducing replacement frequency and increasing productivity for manufacturers.
Overall, the combination of these properties makes titanium a preferred choice for precision tooling in various industries, delivering strength, durability, and reliability.
4. Aluminum
Aluminum is a widely used material known for its versatility and lightweight nature. It is a non-toxic metal that offers excellent corrosion resistance, high thermal conductivity, and low density. Manufacturers love working with aluminum for precision tooling solutions for several reasons.
Firstly, its lightweight property makes it easy to handle, reducing operator fatigue and increasing productivity. Secondly, aluminum’s corrosion resistance ensures the longevity and reliability of precision tools, even in challenging environments. Additionally, aluminum has excellent thermal conductivity, allowing for efficient heat dissipation during machining operations. This property helps to prevent overheating and prolongs the tool’s lifespan.
Furthermore, aluminum is highly machinable, enabling manufacturers to create intricate and precise tool designs. Lastly, aluminum is a cost-effective option, making it an attractive choice for manufacturers.
Collectively, these properties make aluminum the favored material for precision tooling, guaranteeing strength, durability, and reliability across diverse industries.
5. Brass
Brass, an alloy comprised of copper and zinc, is a favored material among manufacturers in precision molding. Its combination of strength, durability, and corrosion resistance makes it highly desirable for this application.
The exceptional machinability of brass allows for precise shaping and molding, enabling the creation of intricate designs with remarkable accuracy. Moreover, brass exhibits excellent thermal conductivity, making it well-suited for heat exchange applications. Its resistance to wear and tear ensures prolonged tool and mold lifespan, reducing the need for frequent replacements and ultimately boosting productivity.
Overall, the unique properties of brass make it a versatile, durable, and reliable choice for precision molding in various industries.
Materials we Process at CAM Resources:
We start by ensuring a strong foundation. Our custom tooling components are manufactured with utmost precision and quality, adhering to the strictest engineering and finishing standards. Using certified raw materials, we tailor our products to meet our valued customers’ exact specifications and requirements.
From precision mold and die sets to components, jigs, and fixtures, we offer a comprehensive range of products that can be delivered worldwide. Predominantly we rely on steel and carbide materials, giving the majority of the spec requirements from our customers.
Our stainless steel range includes SKD11, SKH51, DC53, S45C, S50C, ASP23, ASP30, SUS404, A6061, A5052, ASP23, SKH51, SKD11, PD613, DC53, SKS3, SUS440C, HPM31, HAP40, S45C, S50C and DAC-MAGIC.
On the other hand, the carbide materials include E20, KD20, EF20, RD50, D40, VF12, V10, V20, V30, V40, V50, V60, MC20, G5 and EF10.
Be assured that our material suppliers are very carefully chosen to get the best quality output for our customers, taking into consideration the longevity and cost factors. Check out CAM Resources’ blog to learn some other factors that help maintain the top-notch quality of your molds.
Go With Materials That Best Fit Your Precision Tooling Spec
There is little information about the commonly used materials for precision tooling, however, there are only a few perfect solutions for your business. Knowing about these materials helps you make informed decisions about which materials to use for your specific needs, resulting in higher-quality products and increased efficiency in the manufacturing process.
At CAM Resources, we offer the best materials and products available in the market, designed to help your business achieve maximum productivity and success. Our advanced technology, cutting-edge software, and skilled technicians work together to exceed your expectations, delivering high-quality materials and products that meet your specific needs.
Don’t settle for less than the best. Choose the best materials for your business and watch your productivity soar.
Minh Ngoc Truong
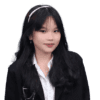
Hi, I'm Minh Ngoc, a dedicated blog writer and social media manager at CAM Resources.