From manufacturing consumer goods to medical devices, injection molding is the most reliable process for the mass production of plastic parts of varying shape complexities with precision and repeatability. With evolving technologies, let’s see how injection molding gears up to meet the modern-day consumer demands, from different perspectives.
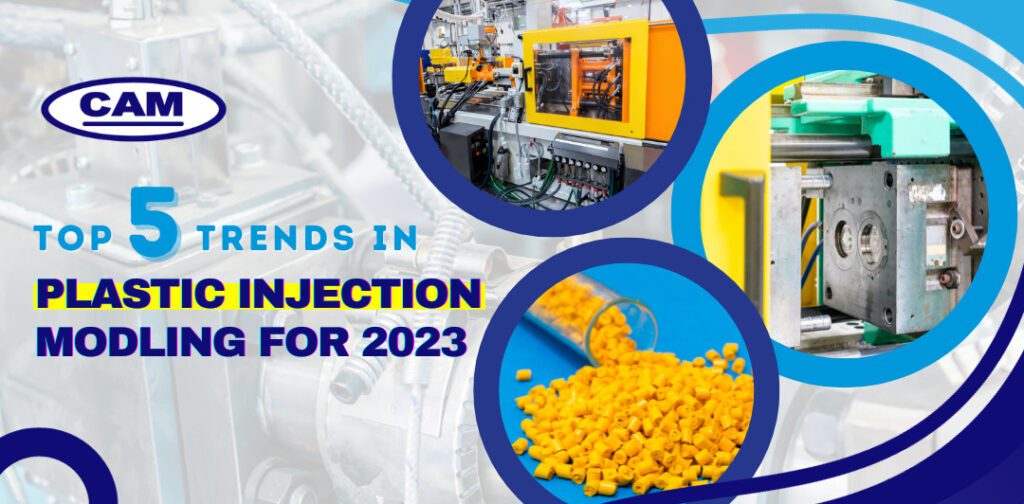
It’s the time of Industry 4.0 and technological innovation in manufacturing takes the driver’s seat bringing us to a new level of productivity, efficiency, and quality standards across the production lines. With that being said, plastic injection molding continues to increase its popularity given its crucial role to play in modern manufacturing.
It’s no surprise that plastic injection molding has become a well-established and integral part of various industries directly contributing to the production of a multitude of plastic parts for our day-to-day usage.
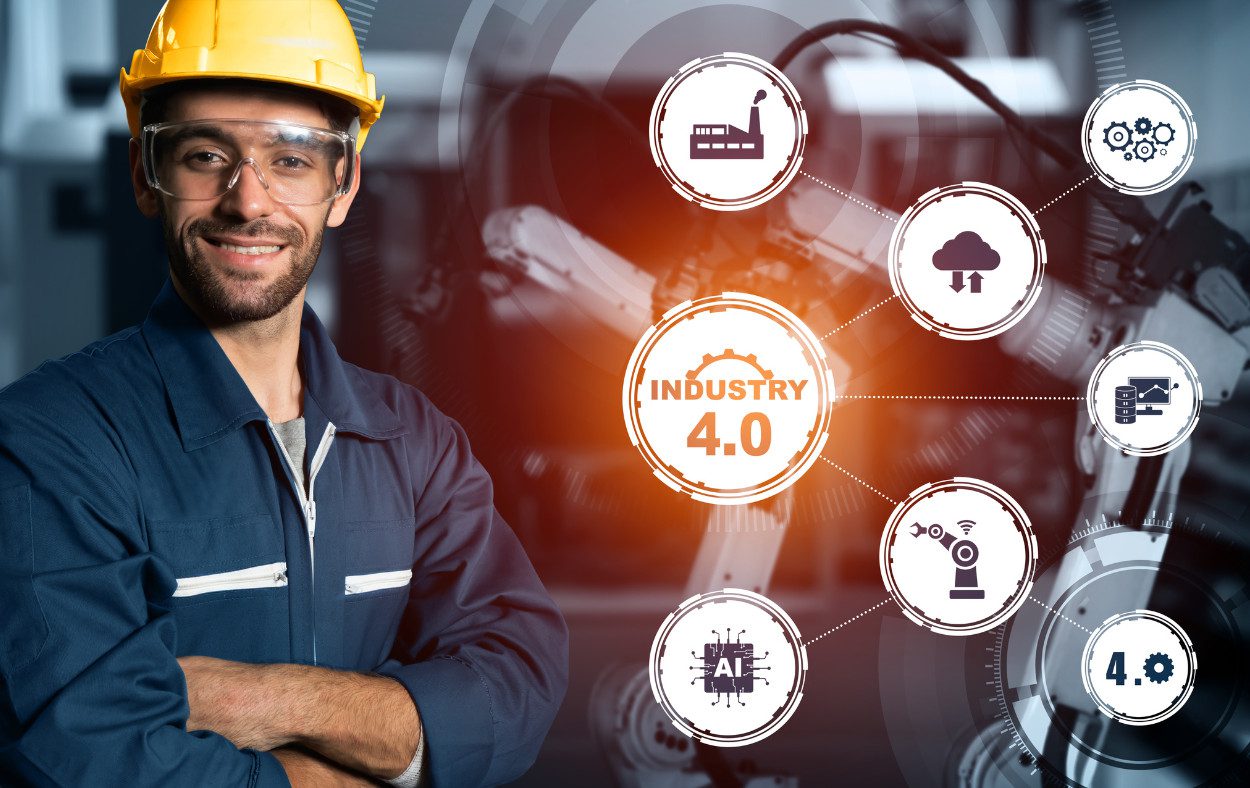
With the constantly emerging technologies and increased cognizance towards the environment, comes the need to meet the modern demands of different industries for injection molding. This has led to innovations and trends that we will run through, in the article.
Significance of Injection Molding:
Plastic injection molding has an instrumental role in the manufacturing process in the modern day for more than one reason. The process is based on the principle of injecting molten plastic material into the mold cavity.
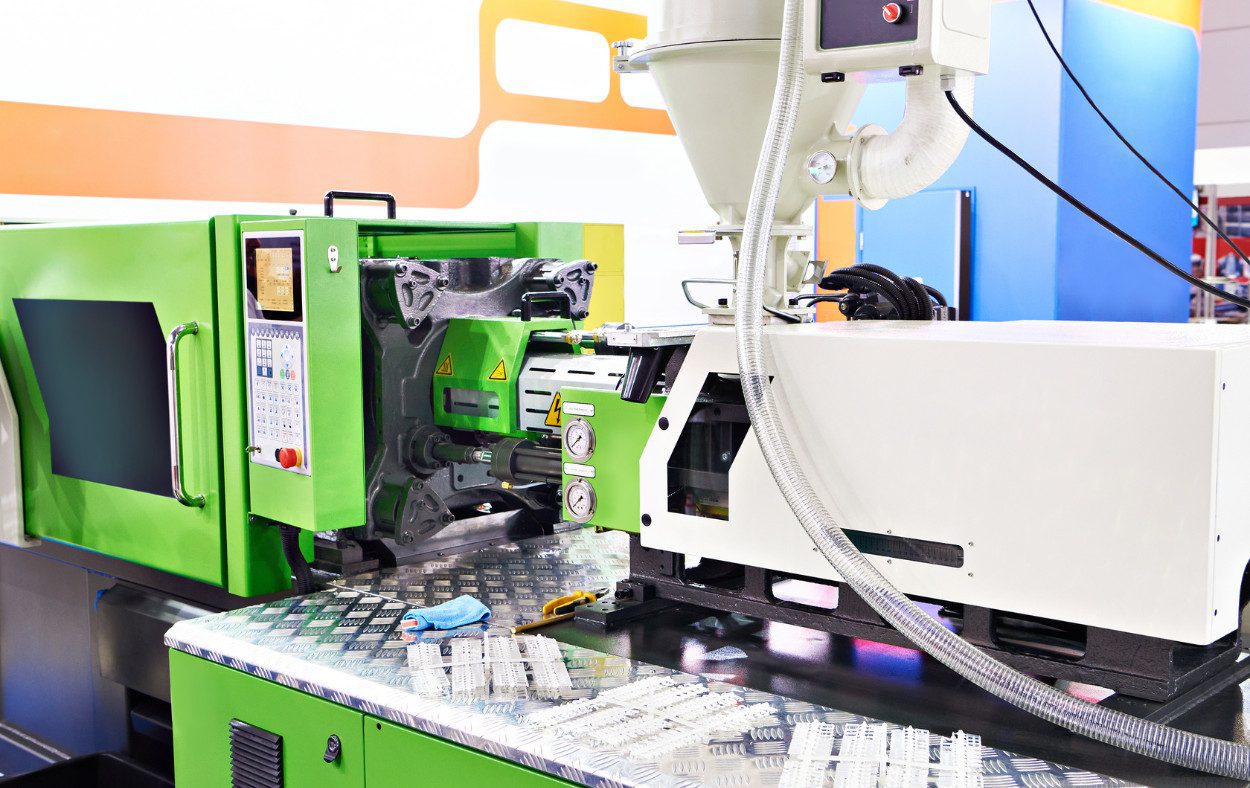
To begin with, the plastic granule raw material is fed through the hopper and the heating unit melts the material that is injected into the mold. Once the material is melted and injected into the mold, it is allowed to cool and solidify, taking the shape of the mold cavity. The mold is then opened, and the solidified part is ejected from the machine. Check out our detailed blog for more insights on how injection molding machine works.
Before we take a peek into the top technological trends of injection molding, let’s run through why it’s highly regarded in the connect of manufacturing, as listed below:
Cost-effective Production:
With custom molds built with absolute precision, plastic injection molding allows high-volume production at a relatively low cost per part with no need for additional post-production work.
Versatility:
Ranging from small components to large parts, plastic injection molding can help produce a wide range of plastic products with varying levels of complexity, offering designers manufacturers the flexibility to create custom-designed products with desired features. Injection molding enables the creation of complex geometries, thin walls, and intricate details that would be otherwise difficult to achieve.
Material Options:
Plastic injection molding supports a wide variety of plastic materials, including thermoplastics and thermosetting polymers. This allows manufacturers to select materials with different properties, such as strength, flexibility, heat resistance, and chemical resistance, based on the specific requirements of the product.
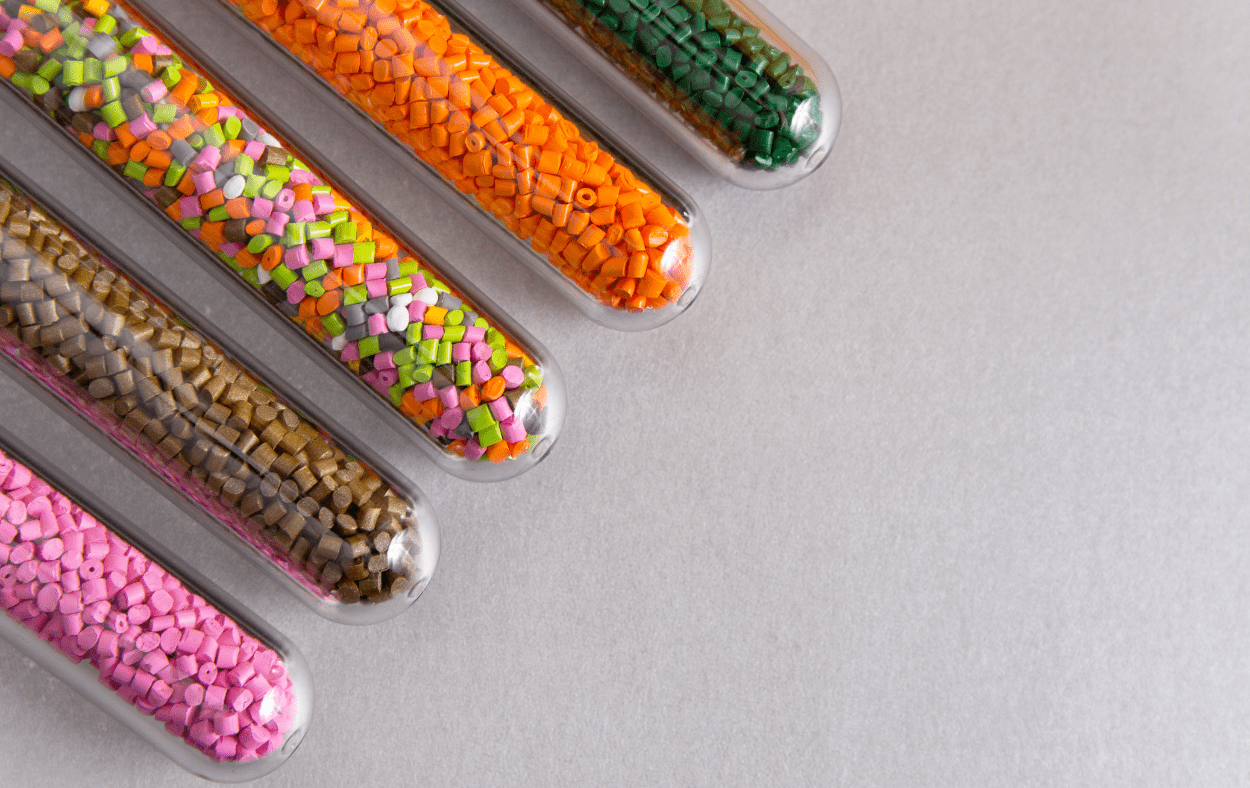
Quality with Consistency:
The injection molding process ensures consistent and repeatable results, leading to high-quality products. The use of computer-controlled machines and advanced molds allows for precise control over factors like temperature, pressure, and cooling time, resulting in consistent part dimensions and improved product quality.
Rapid production: Plastic injection molding enables fast production cycles, with parts being produced within seconds or minutes. The ability to produce large quantities of parts quickly makes it suitable for industries that require high production rates, such as automotive, electronics, and consumer goods.
Waste Reduction:
The injection molding process produces minimal waste as excess plastic can be recycled and reused. The scrap generated during the manufacturing process can be reground and reprocessed, reducing the environmental impact and overall raw-material costs.
Top 5 Trends in Injection Molding to Watch out for:
The promising future of injection molding is propelled by emerging trends that are meant to enhance the outcomes of production, embracing digitalization and sustainability, thus maintaining a competitive edge in the marketplace, besides going green. Here are five such innovations to take note of:
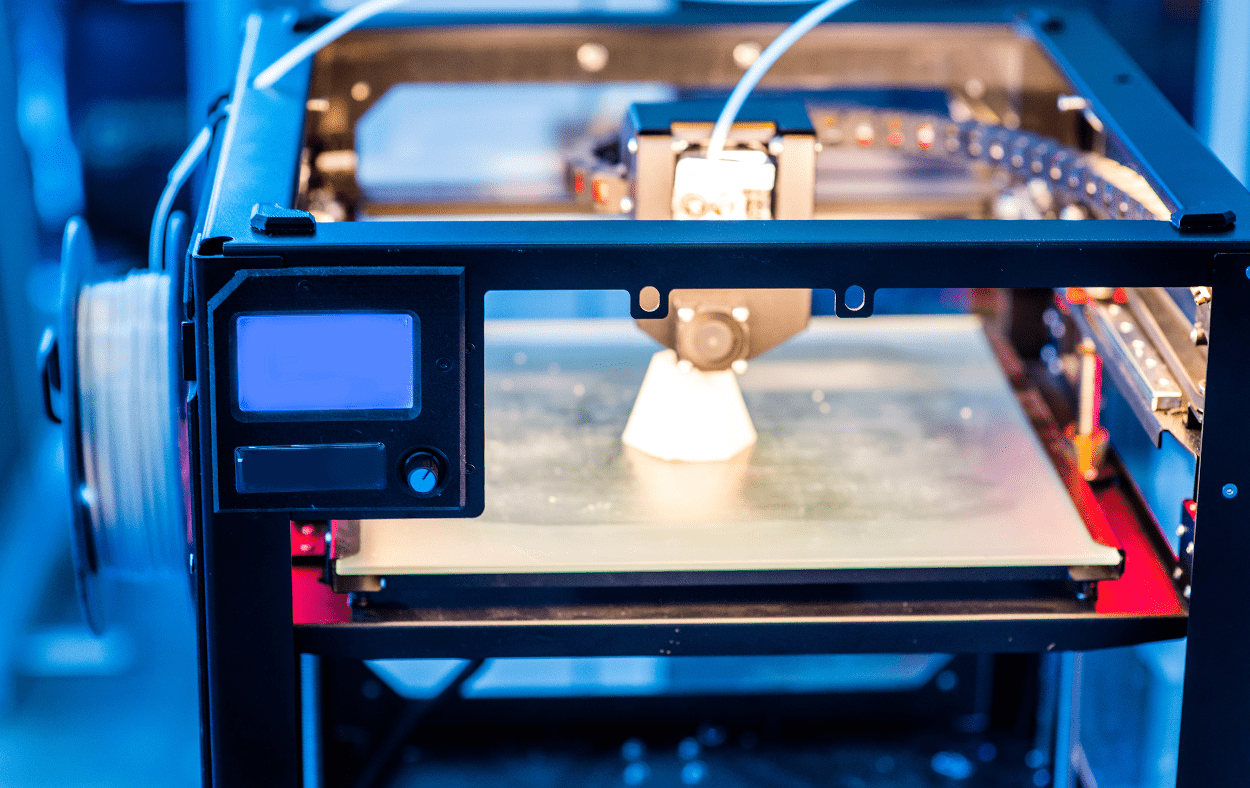
Intelligent Manufacturing:
Intelligent manufacturing has revolutionized the industry, and 3D printing is one of the most significant breakthroughs. The latest technologies in 3D printing have made it possible to produce high-quality finished products in a shorter time frame, featuring faster set-up, low entry cost, and flexibility in dealing with frequent design changes.
The simulation and modeling software tools on the other hand can help to predict the performance of the parts and possible defects based on the material characteristics during teh molding process. Furthermore, these tools are capable of reducing the cycle times and optimizing the tools for plastic injection molding.
Greater Automation:
Boosting automation enhances production efficiency severalfold. In the case of plastic injection molding welcoming the advancements in robotics has a direct impact on production efficiency, labor costs, and product quality.
It’s safe to say that the injection molding sector is in the process of digitalization and manufacturers are adapting to IoT (Internet of Things) and AI technologies. This enables plastic injection factories to run production remotely, monitoring the conditions by digital means and getting alerts and updates as needed.
Cobots aka collaborative robots are more of assisting robots working alongside human machine operators relieving them from repetitive tasks, some of which could be hazardous. All-in-all, these technologies help reduce the risk factors of certain production processes and give a break to the technicians from mundane tasks, with a great turnaround time.
Circular Economy & Sustainability:
Manufacturers from across countries are aiming to develop trends to recycle and reuse plastics better during the production process. The idea is to adapt to a circular economy to reduce waste and pollution and circulate materials and products at their best.
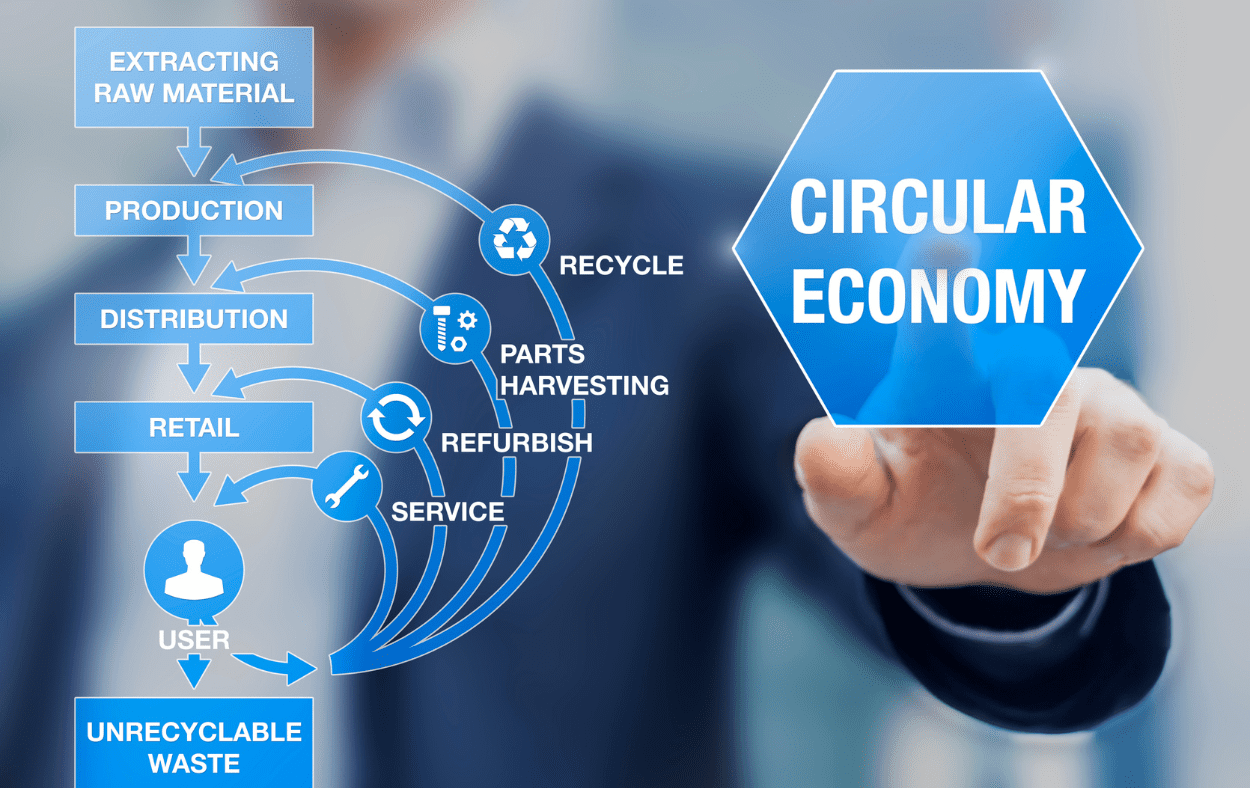
By nature, plastic injection molding makes efficient use of the material, however, the weight control software helps measure and maintain a consistent weight on each shot given the viscosity difference that happens to raw materials after re-granulation
As more manufacturing companies commence to realize the potential of sustainability in injection molding, they are developing thoughtful approaches to product design and production processes, ensuring less waste and enhanced efficiency.
Varying Industry Demands
The injection molding industry is witnessing varying demands driven by different sectors and has to be customized. One significant trend is the surge in demand from the packaging industry, fueled by the growth of e-commerce, for which injection molding offers a cost-effective solution for mass-producing packaging materials such as plastic containers, bottles, and caps.
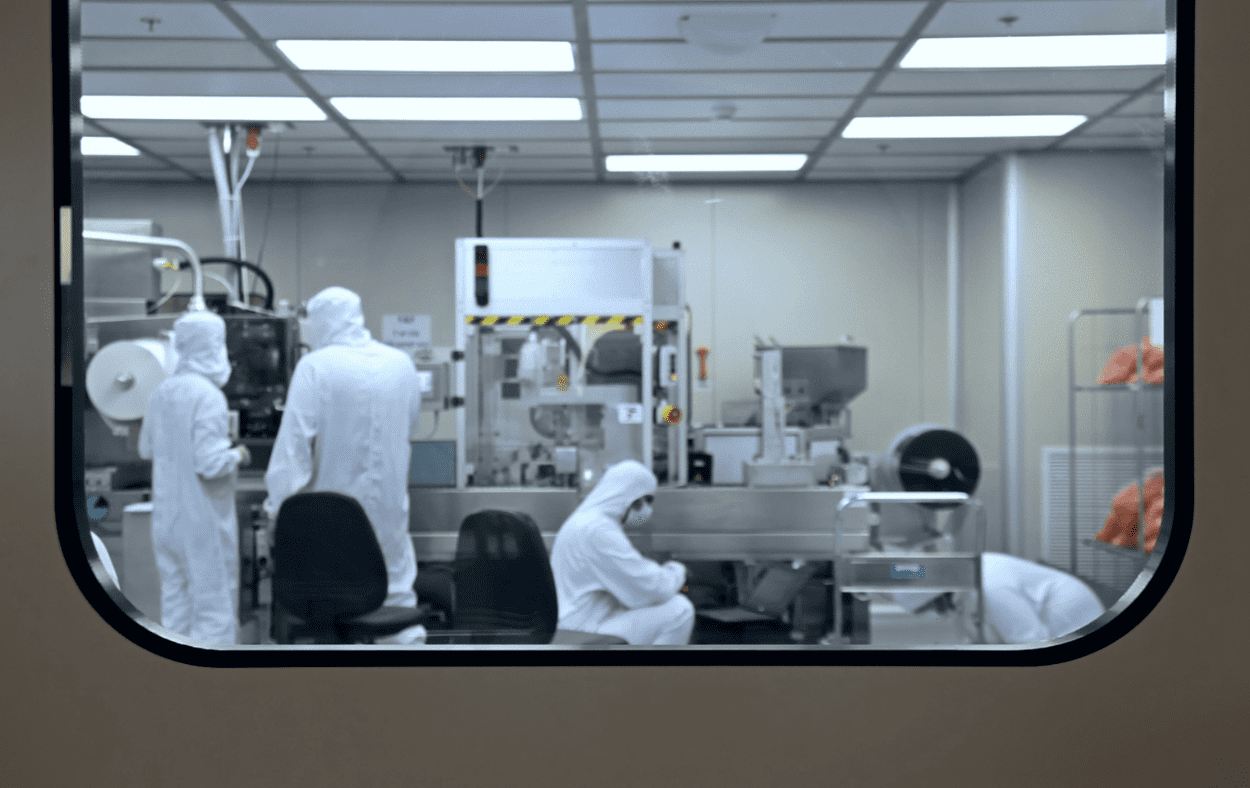
The medical industry is another sector that is driving demand in terms of cleanroom molding, which ensures the production of medical devices and components in a controlled environment, minimizing the risk of contamination. The investment in specialized cleanroom facilities and implementation of stringent quality control measures to cater to the growing demand for cleanroom molded medical products.
Furthermore, the automotive industry is actively seeking innovation in injection molding technology, exploring ways to reduce vehicle weight, improve fuel efficiency, and enhance overall performance. Injection molding enables lightweighting through the use of advanced materials and complex designs. Additionally, integrating functionalities within molded components, such as sensors and electronics, is being explored to enhance safety and connectivity.
Material Durability and Innovation:
Lightweight preference is quite evident from consumers across industries and hence the trend creeps on to injection molding as well. This eventually has a positive impact in terms of transportation, energy efficiency, and product performance.
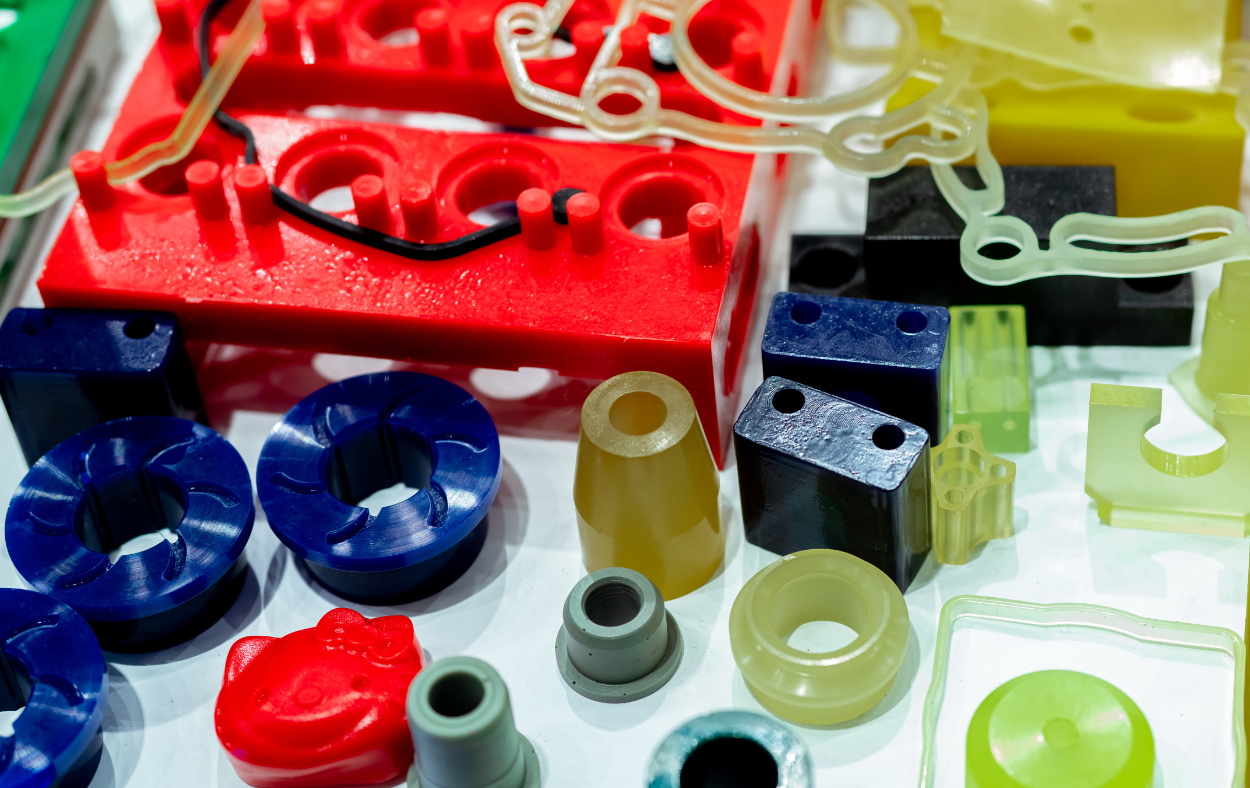
There is a rising consciousness of sustainability and environmentally friendly materials. Hence, Bioplastics as natural alternatives that are carbon-neutral, compostable, and bio-degradable are taking over.
On the other hand, manufacturers are elevating their focus on durable materials that can withstand high temperatures and extremities of production. Thermoset materials and engineered plastics are taking the main stage on this front
RELIABLE PRECISION MOLD SOLUTIONS:
With that being said technological advancements and trends, customization, and personalization are further gaining prominence within the injection molding sectors. Consumers expect new products tailored to their specific needs. Manufacturers hence have to leverage modern technologies including multi-cavity mold and in-mold labeling to produce unique products.
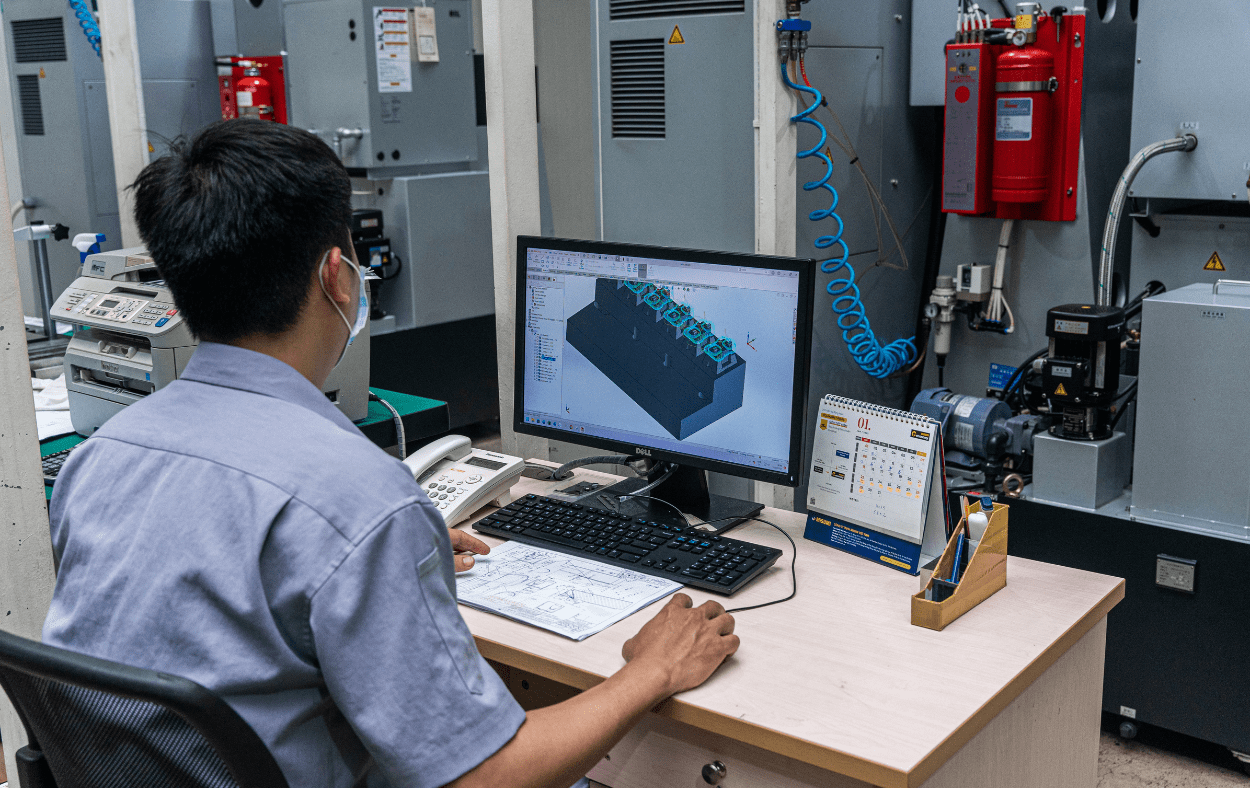
In other words injection molding market technologies constantly keep evolving and demand is often driven by sustainability, customization, innovation, and efficiency. To address these demands, manufacturers of plastic injection molds and precision tooling have to rely on cutting-edge tooling software and machinery and stay on top of the trend, understanding the ever-changing needs of the market.
CAM Resources has about 2 decades of expertise in precision tooling offering a wide variety of mold and die solutions for manufacturers across the globe. Feel free to check our website and send us an inquiry.